1900
Scientific Management
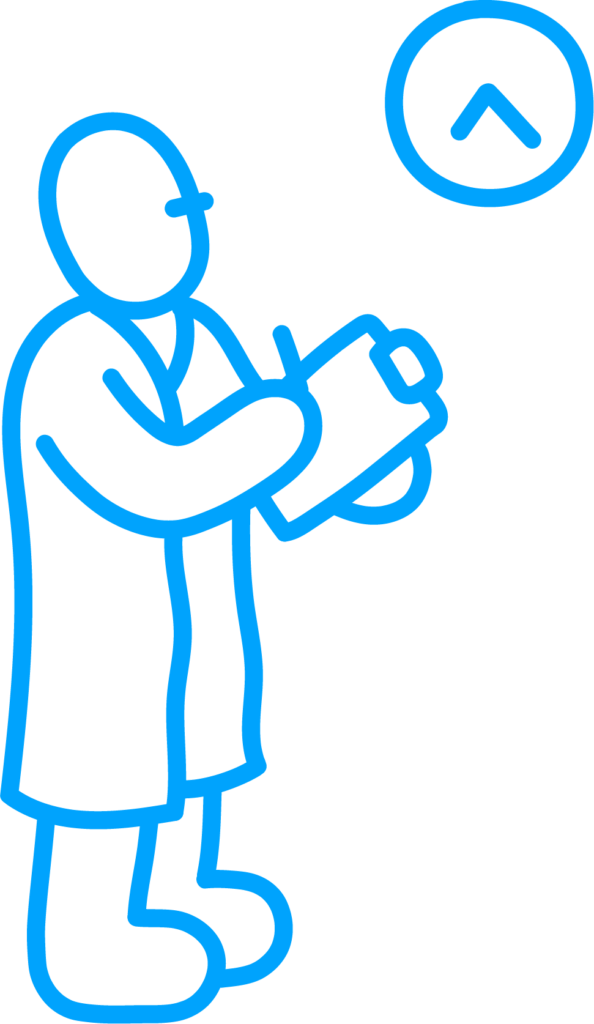
Taylorism
This management theory, developed by Frederick W. Taylor in the early 20th century, focused on optimizing labor productivity through the scientific analysis of workflows. Workers movements were studied, optimized and standardised. The work was clearly divided between management and workers. By breaking tasks into simple, repeatable steps and closely supervising workers, Taylorism aimed to increase efficiency and output.
However, the tasks were highly demanding and their repetitive nature and hierarchical control often reduced workers’ autonomy, leading to dissatisfaction and high turnover rates.
This approach laid the foundation for modern work organisation today, but has been criticized for its dehumanizing effects on workers.
Fordism
Henry Ford applied Taylor’s approach to the mass production of cars using the mechanic assembly line. Tasks were heavily standardised and mechanised within strongly hierarchical structures, which resulted in limited costs and unprecedented gains in productivity. It also led to repetitive and monotonous work for laborers, reducing their autonomy, skills and job satisfaction.
Information Graphics
From the ancient Mesopotamian geometric drawings to the elementary information graphics created by engineer William Playfair, graphic formats have consistently been closely associated with economics. The industrialisation not only standardised work practices but also drove the standardisation of graphic formats to facilitate the bureaucratisation of work processes. Information graphics like charts and diagrams were instrumental in visualising data and streamlining workflows.
1950
Lean
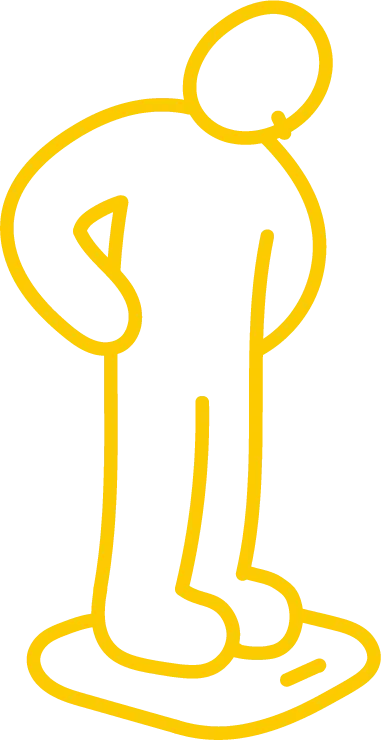
Total Quality Management
The ideas of total quality management were developed by William Deming after World War II and formed the basis of lean approaches. It focuses on continuous improvement, customer-centricity, and quality control throughout an organization.
Toyota Production System
This system was developed during the 1950s at Toyota in Japan and builds on various principles established by taylorism and fordism, such as a centralisation of planning, the division of labour and the use of the assembly line. It focuses on maximizing efficiency and minimizing inventory and waste through lean manufacturing principles. It emphasizes just-in-time production (JIT), where products are produced only as needed, and continuous improvement (Kaizen) involving all employees. Flexibility, high quality, and customer centricity are promoted. It has been labelled as “lean production” in 1990.
Lean management
The ideas of total quality management were developed by William Deming after World War II and formed the basis of lean approaches. It focuses on continuous improvement, customer-centricity, and quality control throughout an organization.
1990
Agile
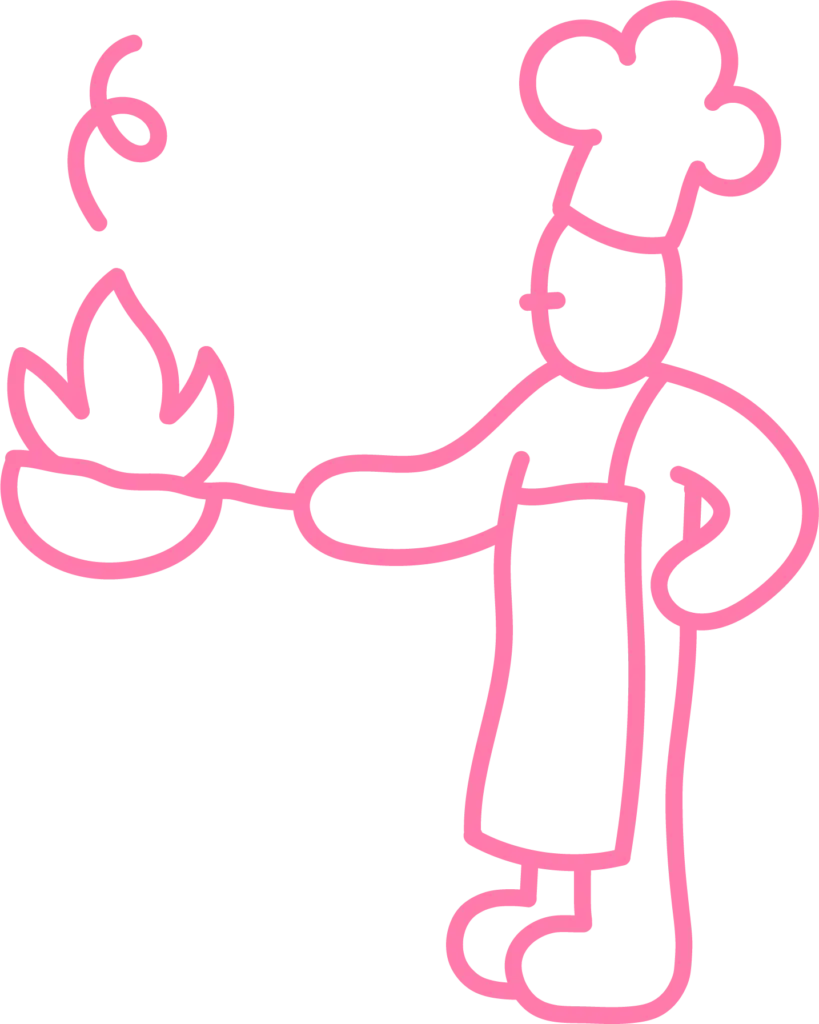
PDCA Cycle
The foundations of agile methodologies were laid long before the term ‘agile’ was coined. Similar to lean principles, the ideas of total quality management form the basis of agile approaches.
In particular the PDCA (Plan-Do-Check-Act) cycle, which promotes continuous improvement through iterative planning and refinement. In this cycle, teams plan a change, implement it on a small scale with little effort as prototypes, observe and analyze the results, and then act based on the findings. The basic idea is to avoid long-term planning by concentrating on short-term planning of small project phases.
New Work
In the 1980s, philosophy professor Frithjof Bergmann coined the term “New Work.” He critiqued the Taylorist capitalism of automation and advocated for work that empowers and energizes individuals. Bergmann envisioned an alternative economic system and a new work culture fostering competence, meaningfulness, and independence. Although the term is ubiquitous today in the context of agile work, it has largely been stripped of its critical stance and has become a generic term for democratized leadership or digital remote work.
The Agile Manifesto
In 2001, 17 software developers convened in Snowbird, Utah, to conceptualize their experiential insights in response to their frustration with traditional preplanned and hierarchical project management, which was referred to as the “Waterfall” approach. This meeting resulted in the Agile Manifesto, a declaration of four core values tailored to self-managed multidisciplinary teams.
Agile emerged as an umbrella term for various methods and frameworks, like Scrum, DevOps, and Design Thinking. They prioritize flexible adaptation to change, iterative development, self-organised collaboration and customer-centricity. Visual tools play a fundamental role in enhancing transparency and communication.
Agile frameworks have been successfully adapted to various industries beyond the IT sector. Many of its elements can be found in the interface and user experience of contemporary project management software.