Concepts
Taylorism
Process
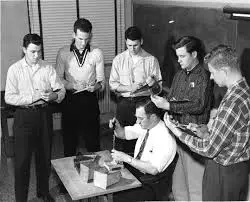
At the beginning of the 20th century, the american engineer Frederick W. Taylor developed a systematic theory about the organisation of work based on the need for increased efficiency in the manufacturing industry, often referred to as Taylorism. It focused on optimizing labor productivity through the scientific analysis of workflows. Workers movements were studied, optimized and standardised. Work was divided with the introduction of specialised planning departments. By breaking tasks into simple, repeatable steps and closely supervising workers, Taylorism aimed to increase efficiency and output. This model was quickly adapted, distributed and established the foundation for modern workplace management.
Comments
Trade unions argued that workers were deprived of their skills and control over their work. They opposed the idea that an autocratic management should have sole authority over work processes, wages, and working conditions, which resulted in workers having no influence on their work environment.
The fragmentation of work with a focus on the „one right way“ increased the division of labor and inhibited intellectual development, which is in conflict with contemporary ideals that promote individual autonomy and responsibility.
Software Analogies
Analogies
Modern project management software tools incorporate taylorist principles such as task standardization, time tracking and centralized planning to enhance efficiency and productivity. These tools also utilize features for performance monitoring, workflow optimization, and detailed documentation
Fordism
Process
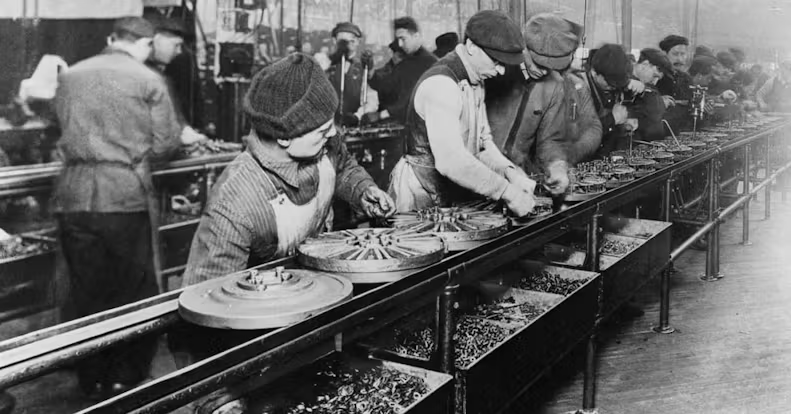
Henry Ford applied Tayloristic principles to the production of cars in the Ford Motor Company. This approach established mass production and is referred to as Fordism. The factory work was mechanised to the greatest extent possible, with workers primarily responsible for operating machines. The standardised tasks required no specific qualifications as they were designed to be simple and highly repetitive. Workers operated with minimal autonomy within strongly hierarchical structures. Planning, control, and quality assurance were centralised in specialised units. The invention of the mechanic assembly line in 1913 ensured a consistent speed, leading to unprecedented gains in productivity.
Comments
The monotonous and high-paced nature of tasks often led to worker dissatisfaction, high turnover rates, and significant physical and mental health issues such as stress, musculoskeletal problems, alienation and depression.
Software Analogies
Analogies
Fordism is reflected through the use of standardized processes, task specialization, and assembly line-like workflows. Modern tools emphasize efficiency and scalability by automating repetitive tasks and ensuring consistency across large teams.
Principles
Centralised Planning
Process
Work was divided with the introduction of centralised planning departments. White-collar managers were responsible for planning and training, while workers solely focused on executing their assigned tasks. This division aimed to enhance efficiency and control, ensuring that tasks are performed in the most effective manner according to pre-determined standards and schedules.
Software Analogies
Centralized Dashboards
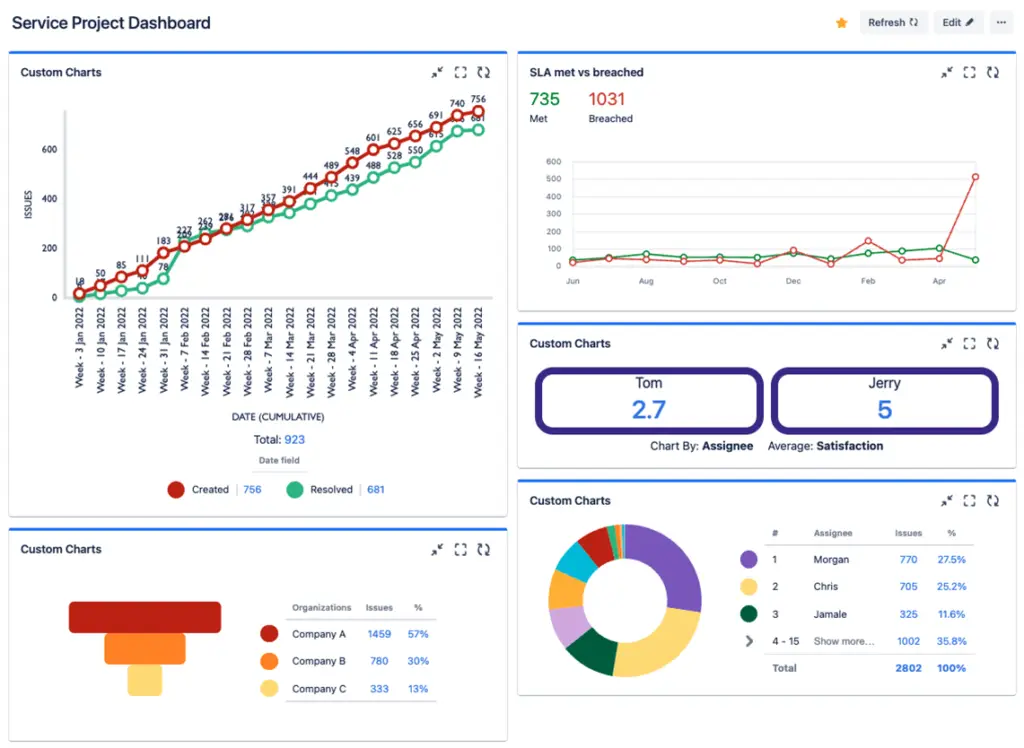
Dashboards provide managers with a comprehensive overview of project progress, enabling efficient monitoring and control.
Centralized Dashboards
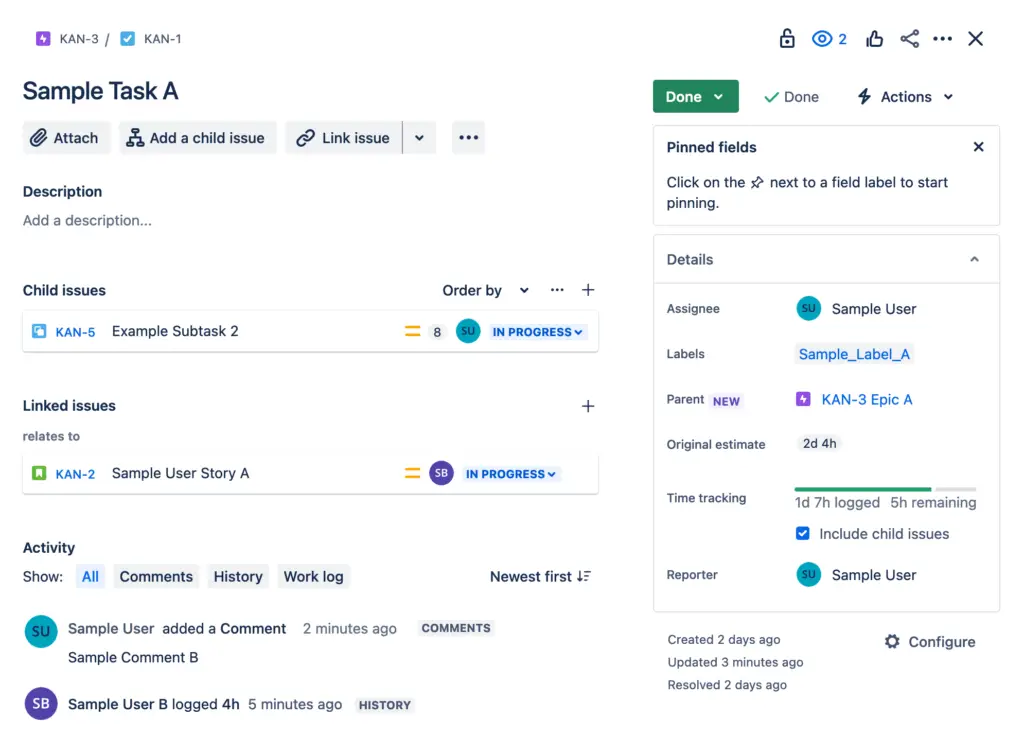
Managers assign tasks to team members, allowing for detailed planning and enabling team members to focus on executing their specific responsibilities according to the centralized plan.
Standardisation
Process
Standardization, a key principle in Scientific Management, involves creating uniform procedures to ensure consistency and efficiency. It defines the “one best way” to perform tasks for precise optimization. Fordism expanded this through large-scale assembly line production, enhancing productivity and uniformity. This approach reduces errors, improves quality control, and simplifies training, making it easier to manage complex operations.
Software Analogies
Project Templates
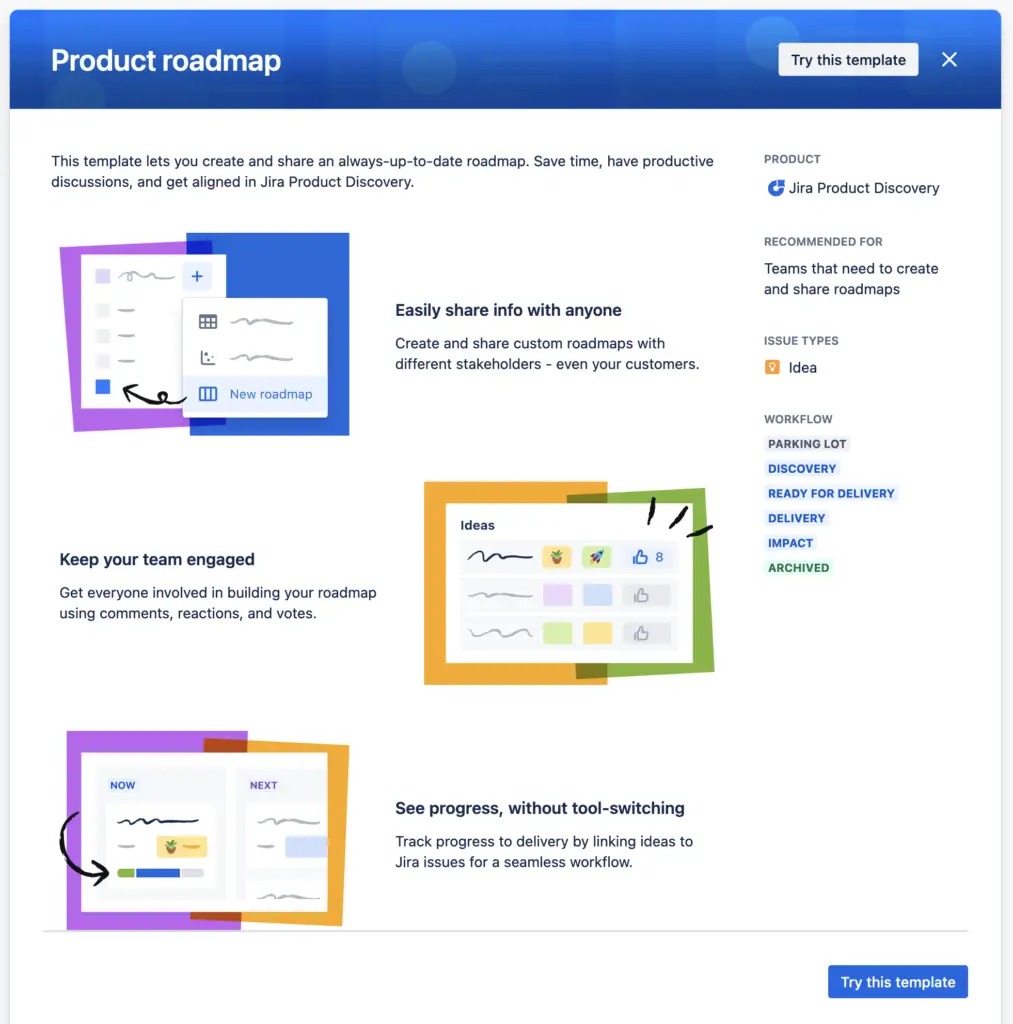
Templates standardize processes, ensuring consistency across different projects by providing predefined workflows and structures.
Automation
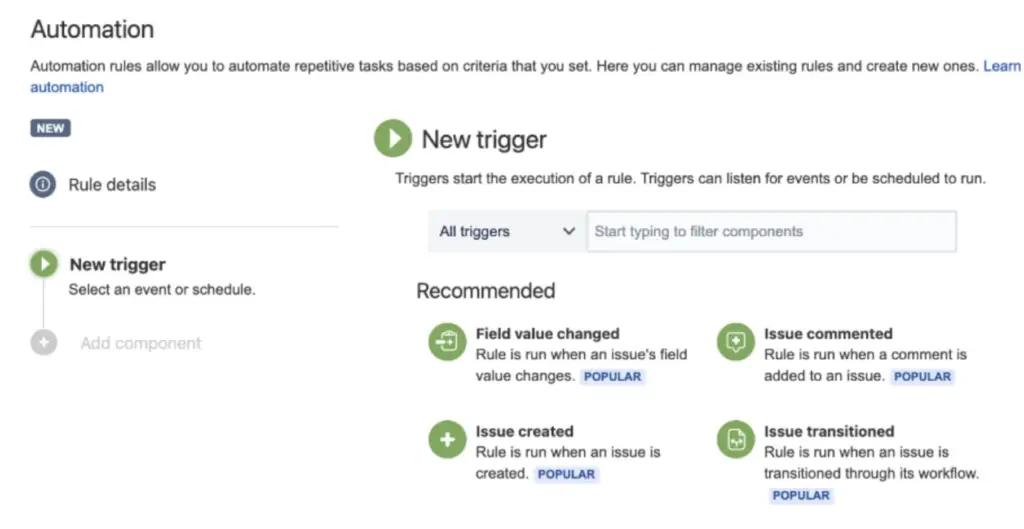
Automated processes and rules reduce variability and errors, maintaining uniform task execution.
Division of Labor
Process
Division of labor involves breaking down work into specialized tasks performed by different workers, enhancing efficiency and productivity. This approach allows workers to develop expertise and reduces the time needed to switch tasks. In Fordism, this was applied on a large scale through assembly lines, where each worker repeatedly performed a specific task, increasing production speed and consistency.
Comments
The fragmentation of work with a focus on the „one right way“ increased the division of labor and inhibited intellectual development, which is in conflict with contemporary ideals that promote individual autonomy and responsibility.
Software Analogies
Task Assignment
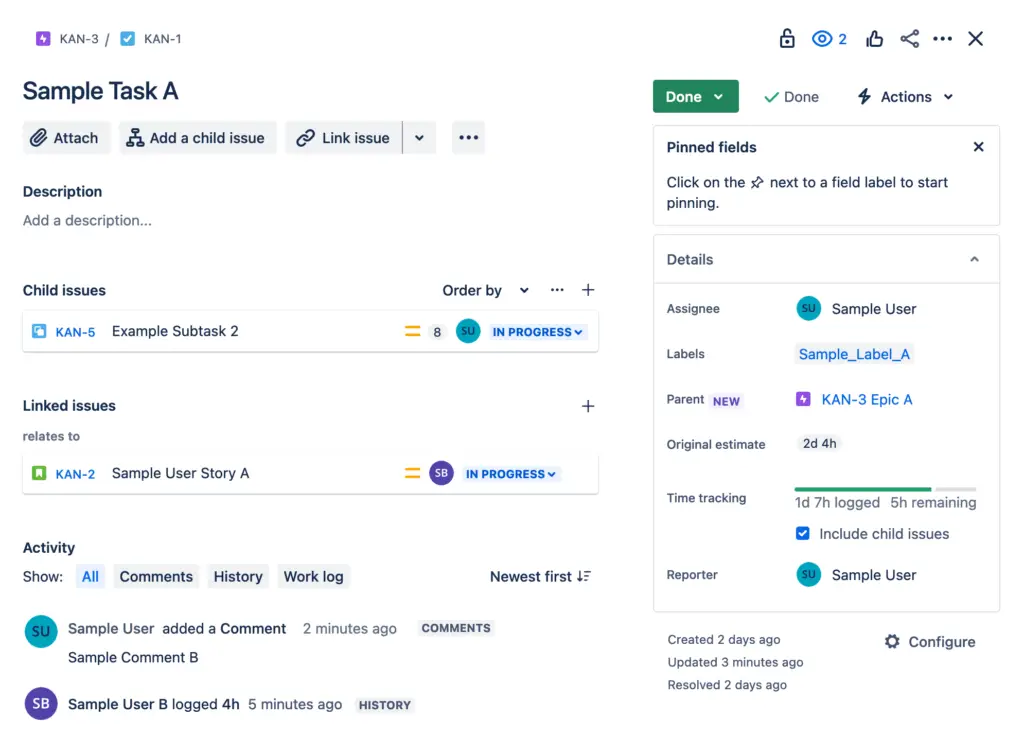
Project management tools allow managers to assign specific tasks to team members based on their expertise.
Role-Based Access
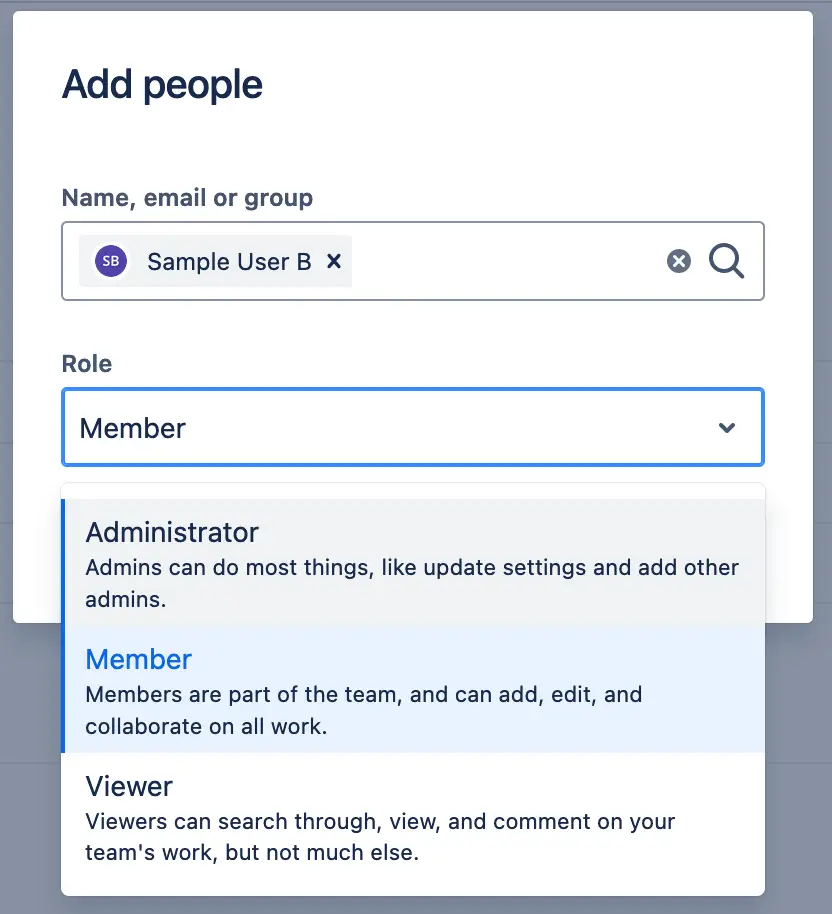
Software systems provide role-based access, ensuring that team members only see and interact with tasks relevant to their roles.
Mass Production
Process
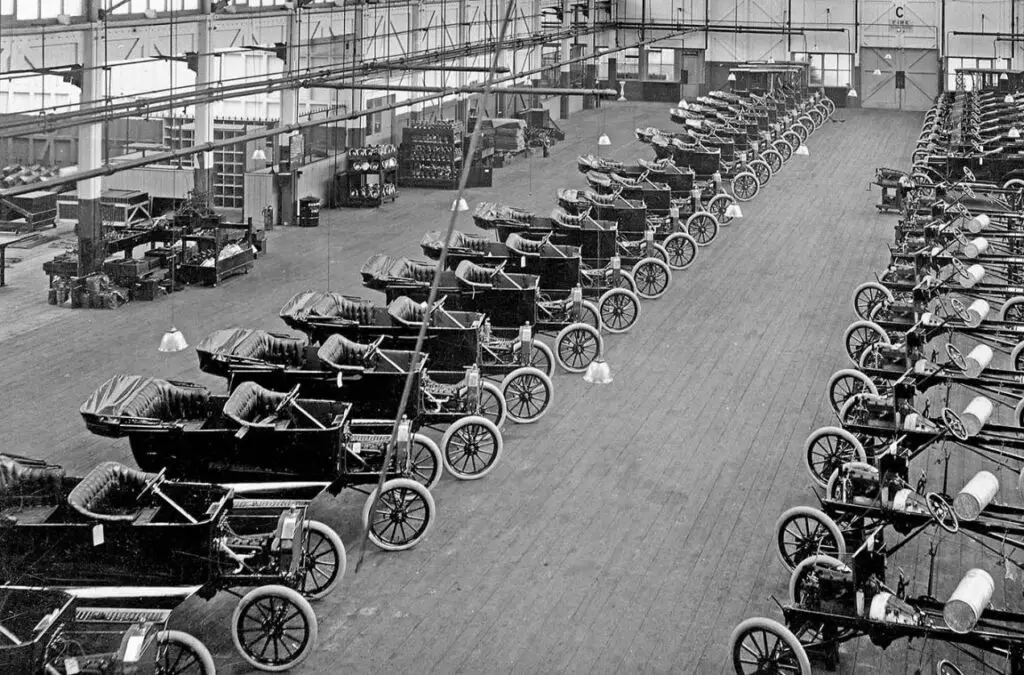
Mass production involves the efficient manufacturing of large quantities of standardised products. In Fordism, this was achieved through the use of assembly lines, where each worker performed a specific, repetitive task in a standardised way.
Methods
Time & Motion Studies
Process
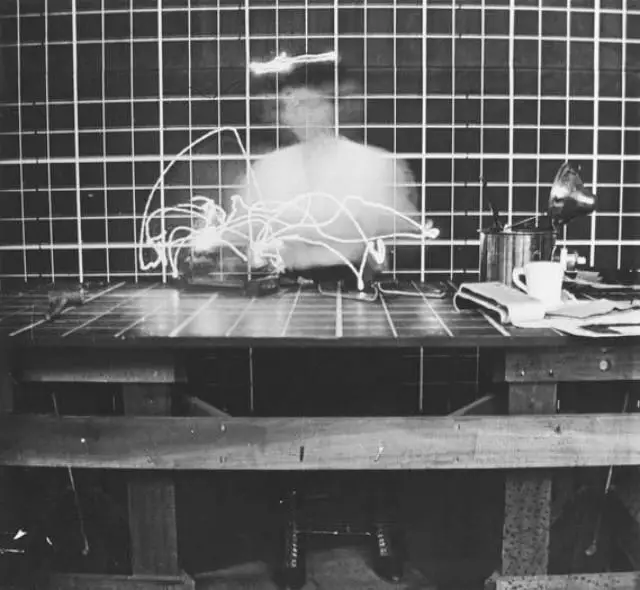
Time and Motion Studies, developed by Frederick W. Taylor and further refined by Frank and Lillian Gilbreth, focus on analyzing and optimizing work processes to enhance efficiency and productivity. These studies meticulously examine each step in a task to identify the most effective form of execution, setting optimal standart times, minimizing unnecessary motions, and establishing standardized best practices.
Sub-Tasks
Time Tracking
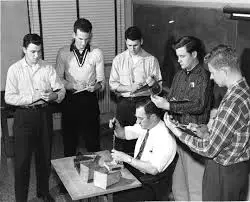
Frederick Taylor used stopwatches to measure the duration of each step in a task to establish standard times for each activity. This ensured that work was carried out as efficiently as possible and that slower workers were highlighted immediately.
Therbligs
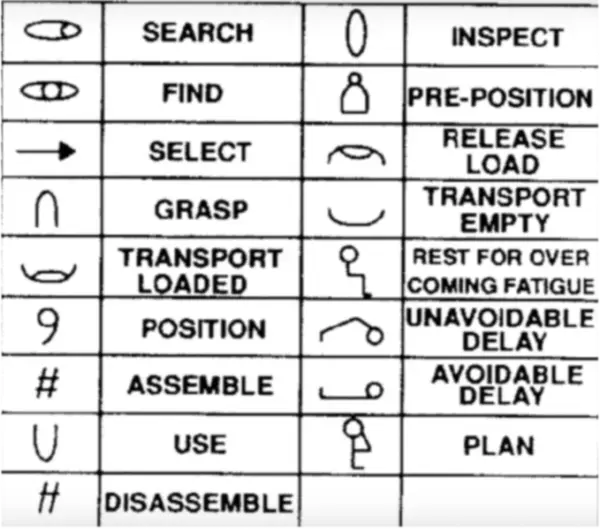
Frank and Lillian Gilbreth expanded on Taylor’s principles by developing the concept of “therbligs,” which are the basic units of motion involved in a task. Each therblig represents a specific action, such as grasping, holding, or releasing. By analyzing and standardizing these motions, the Gilbreths sought to minimize unnecessary movements and streamline work processes.
Chronocyclegraph
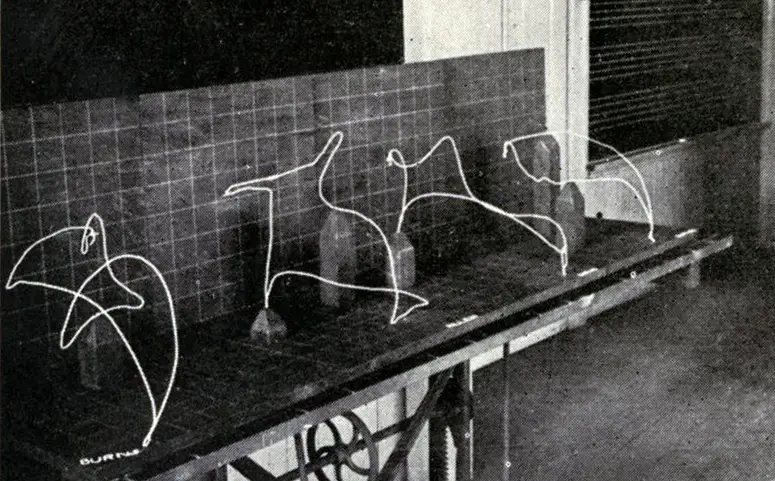
The chronocyclegraph technique, invented by the Gilbreths, involved attaching small lamps to workers’ hands and using time-lapse photography to capture their movements as light trails. These were subsequently transformed into wire sculptures, representing the motions as tangible paths. These trails were analyzed to determine the most efficient sequence of gestures for a given task.
Comments
While time and motion studies significantly enhaced productivity and theoretically reducing worker fatigue, the rigid control and close observation were often perceived as humiliating and intimidating by workers. These practices contributed to the dehumanization of labor, reducing workers to mere robotic cogs in the industrial machine.
Software Analogies
Time Tracking
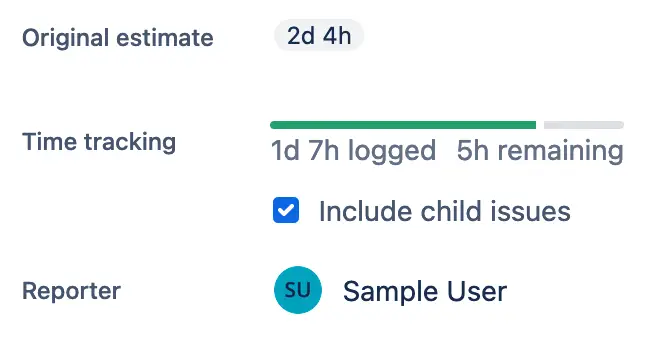
Tools monitor task durations to set performance benchmarks, similar to Taylor’s stopwatch studies.
Workflow Visualisation
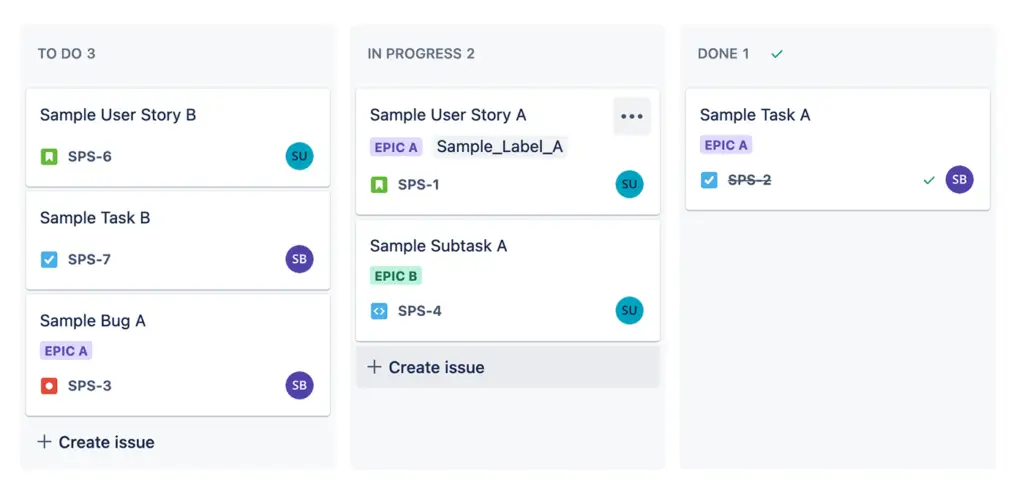
Kanban boards and Gantt charts provide visual representations of workflows, akin to the Gilbreths’ chronocyclegraph.
Efficiency Metrics
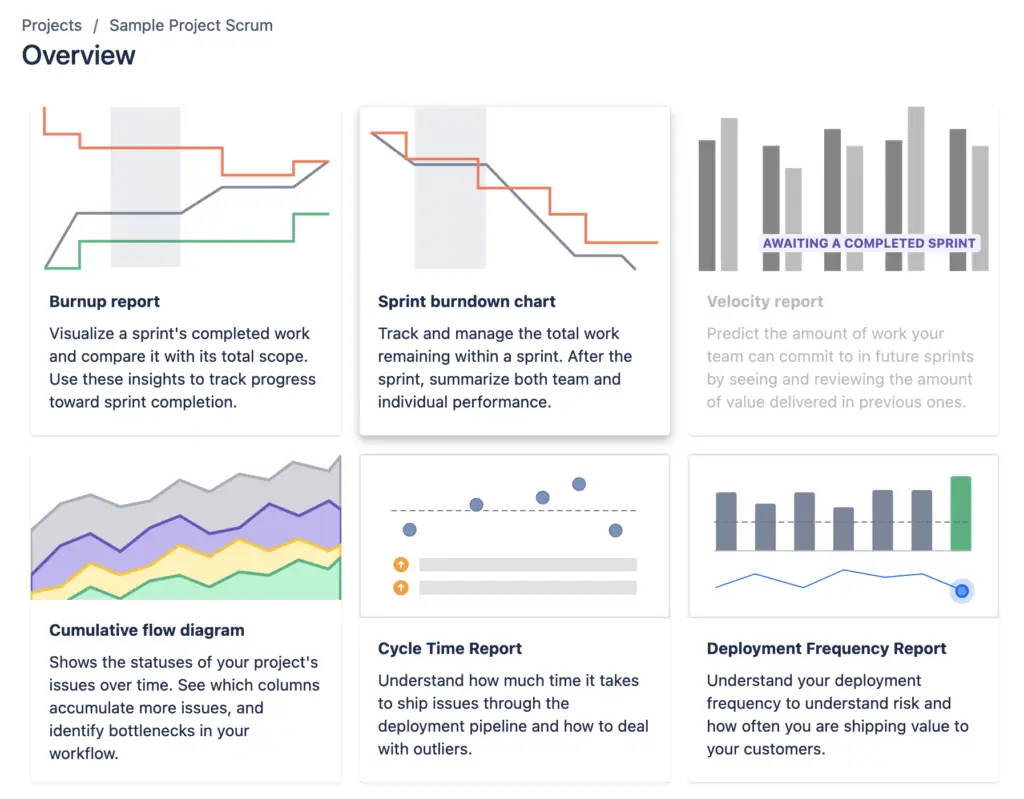
Dashboards and reports offer performance data to improve processes.
Autocratic Leadership
Process
In both Fordism and Taylorism, an autocratic leadership was used as a method to maintain control and ensure efficient workflow. This strong hierarchical structure placed the centralised management at the top, responsible for planning, decision-making, and supervision, while workers were positioned at the bottom, focusing solely on executing tasks.
Comments
The strong hierarchy often led to worker dissatisfaction due to the lack of autonomy and limited opportunities for input or decision-making. Low control of workplace conditions combined with high demands increased the risk of stress-related problems, such as coronary diseases.
Software Analogies
Centralised Dashboards
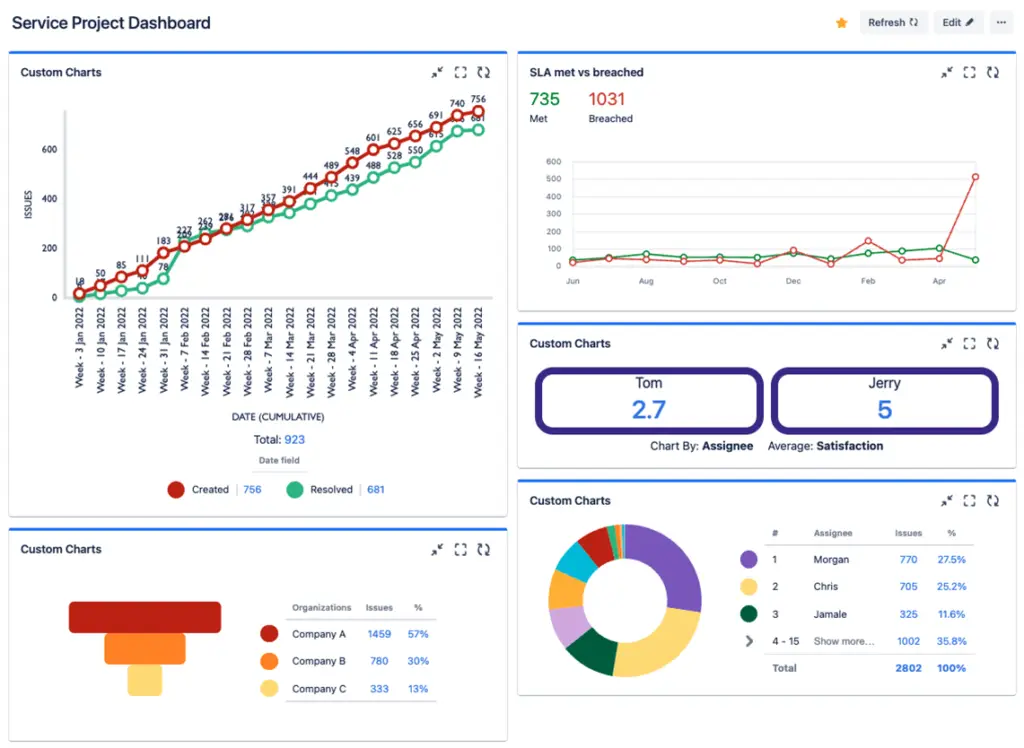
Dashboards provide managers with comprehensive oversight of project progress.
Role-Based Access Control
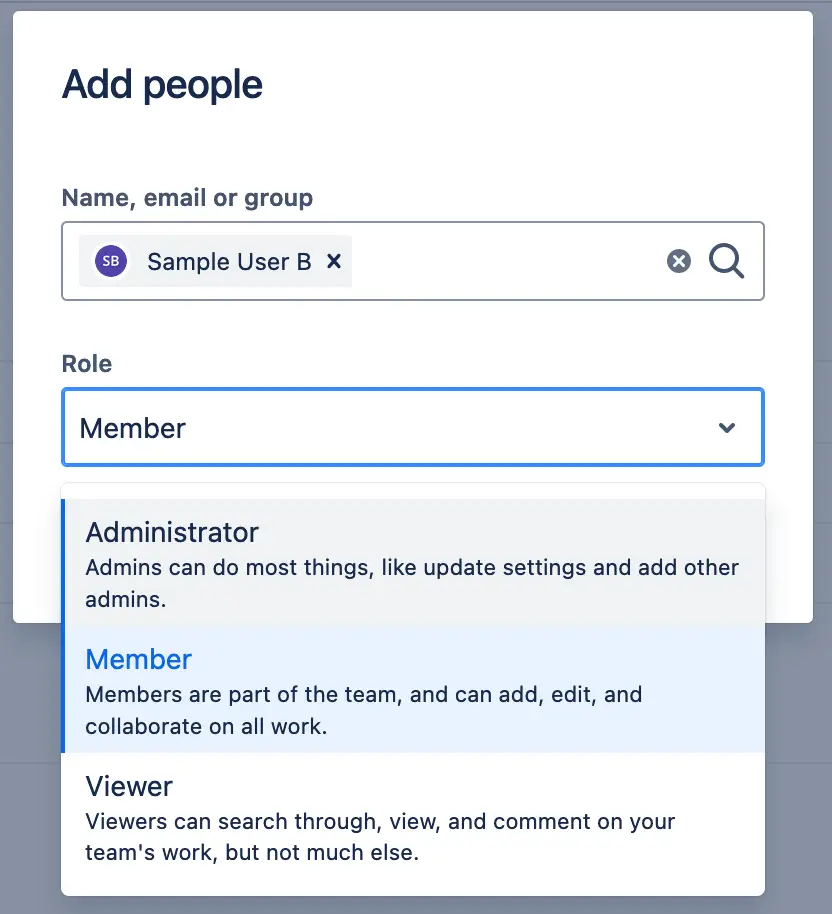
Ensures different levels of access and permissions based on hierarchy, maintaining clear distinctions between management and worker responsibilities.
Task Approval
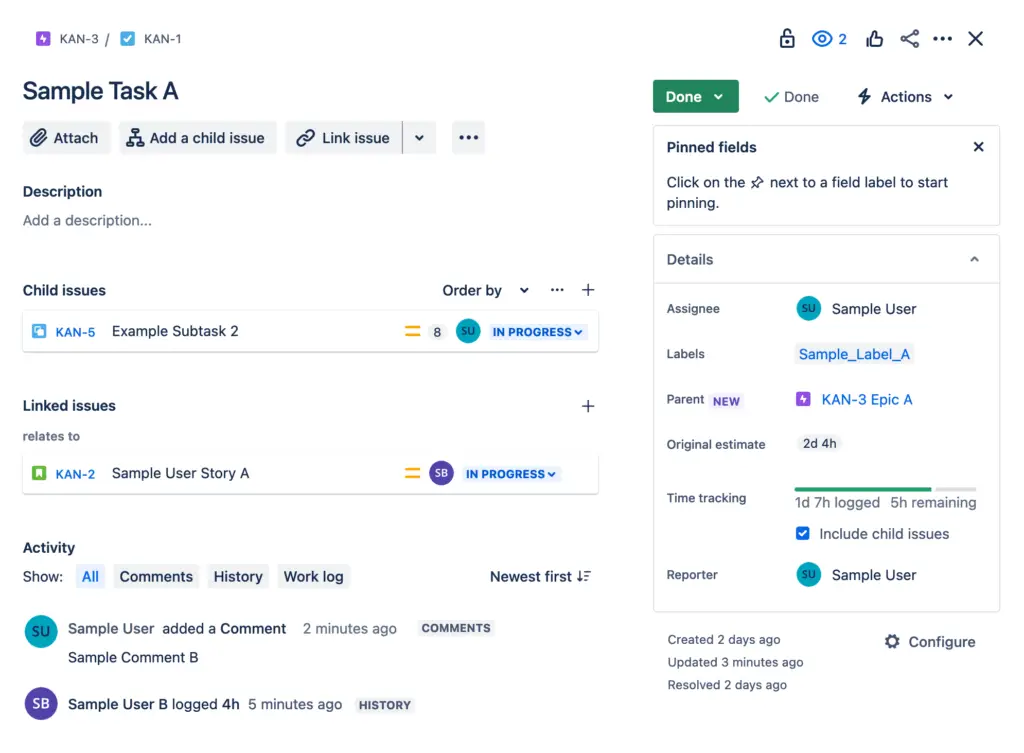
Tasks often require managerial approval before proceeding, mirroring hierarchical decision-making processes.
Assembly Line
Process
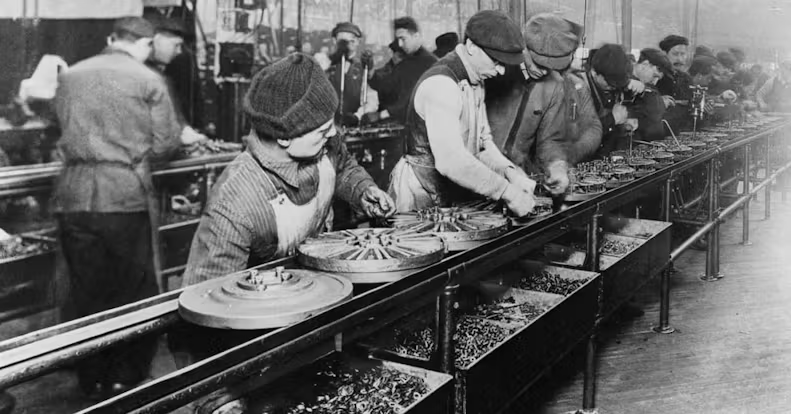
Introduced in the Ford factory in 1913, the assembly line was a cruicial instrument in mass production. It divided the manufacturing process into simple, repetitive tasks performed by specialised workers and set the pace for their completion.
Comments
The assemly line imposed a relentless work pace and made any kind of lagging visible. The monotonous nature of work steps often led to significant physical and mental health issues. Workers lost control over their work because they could no longer determine the velocity themselves.
Software Analogies
Task Automation
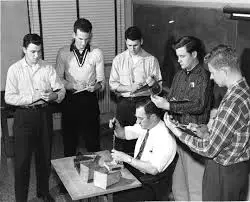
Streamlines processes by automating repetitive tasks. Repetitive tasks and actions can be automated by setting specific conditions.
Task Sequencing
The process of arranging tasks in a specific order to ensure they are completed efficiently and logically. This involves identifying dependencies between tasks, setting priorities, and scheduling tasks in a way that optimises workflow and reduces delays.
Information Graphics
Process
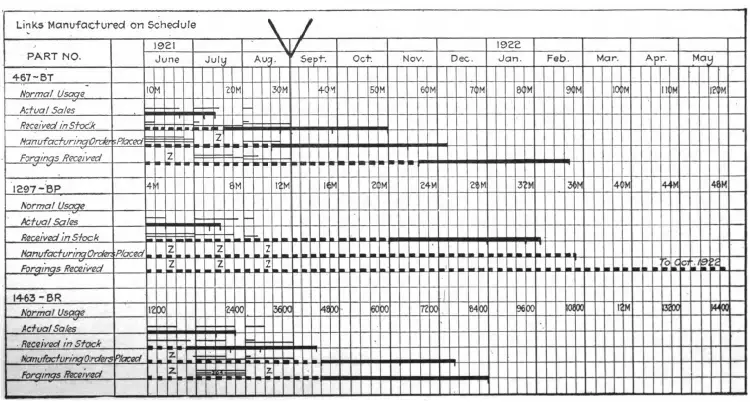
The industrialisation not only standardised work practices but also drove the standardisation of graphic formats to facilitate the bureaucratisation of work processes. Information graphics like charts and diagrams were instrumental in visualising data and streamlining workflows.
In the 1910s, Henry Gantt, an American engineer and management consultant,
popularized the Gantt chart, an elementary bar chart that represents project schedules as horizontal lines, showing deadlines and dependencies of various elements. Tools like the Gantt Chart enable the detailed tracking and scheduling of tasks and are still fundamental components of today’s software tools.
Comments
While these abstract visualisations communicate a great deal in terms of utility and efficiency, they obscure the human element from work processes and leave no room for workers‘ health and social relations.
Concepts
Lean Production
Process
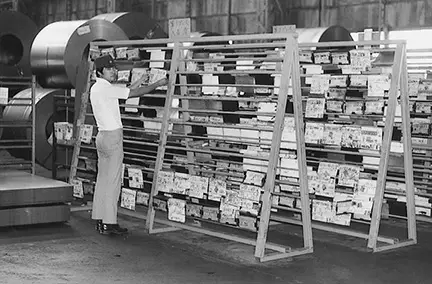
Lean production focuses on maximizing efficiency and minimizing waste in manufacturing processes. The term was coined in 1990, but it is based on Toyota Production System, which was developed during the 1950s at Toyota in Japan. It emphasizes continuous improvement, just-in-time production (JIT), and the elimination of non-value-adding activities. By streamlining workflows and involving all employees in the improvement process, lean production aims to deliver high-quality products efficiently and responsively to customer demands.
Comments
The JIT system‘s intense focus on efficiency and the elimination of buffers and rest periods often leads to high stress levels and increased work pace, which has been referred to as „management by stress“ or „high-fordism“. Competition, emotional manipulation, visual control and intense monitoring may cause feelings of exploitation.
Lean Management
Process
Lean Management, derived from lean production, focuses on maximizing efficiency and minimizing waste throughout the production process. It integrates principles like just-in-time production and continuous improvement, involving all employees in the process. Lean Management aims to create streamlined workflows, reduce inventory, and ensure every step adds value. By generalising the lean concepts principles, it can be applied to the management of basically all types of businesses and organisations.
Comments
The constant push for waste reduction and continuous improvement can lead to high stress and burnout among employees. The just-in-time production method can result in supply chain vulnerabilities, making the system fragile and less resilient to disruptions.
Principles
Customer Centricity
Process
Lean focuses on delivering maximum value to customers by understanding and meeting their needs and preferences. This principle involves engaging customers in the development process, gathering feedback, and making continuous improvements to products and services based on customer input. Lean practices aim to ensure that all activities add value from the customer’s perspective.
Software Analogies
User Experience (UX) Design
Agile frameworks engage customers throughout a software development process to ensure their needs are met.
Value Stream
Process
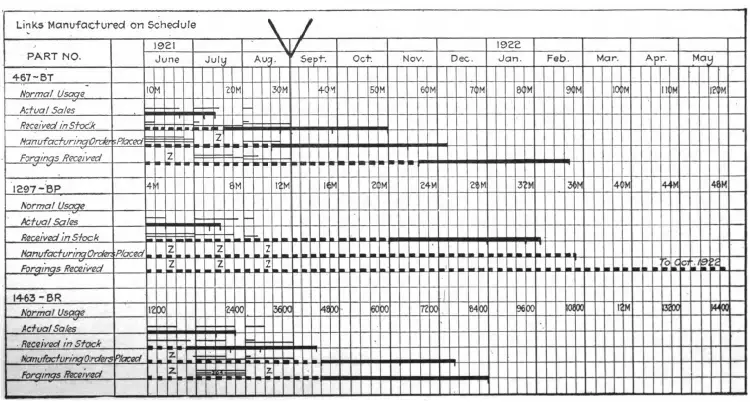
The industrialisation not only standardised work practices but also drove the standardisation of graphic formats to facilitate the bureaucratisation of work processes. Information graphics like charts and diagrams were instrumental in visualising data and streamlining workflows.
In the 1910s, Henry Gantt, an American engineer and management consultant,
popularized the Gantt chart, an elementary bar chart that represents project schedules as horizontal lines, showing deadlines and dependencies of various elements. Tools like the Gantt Chart enable the detailed tracking and scheduling of tasks and are still fundamental components of today’s software tools.
Comments
While these abstract visualisations communicate a great deal in terms of utility and efficiency, they obscure the human element from work processes and leave no room for workers‘ health and social relations.
Software Analogies
Value Stream Mapping
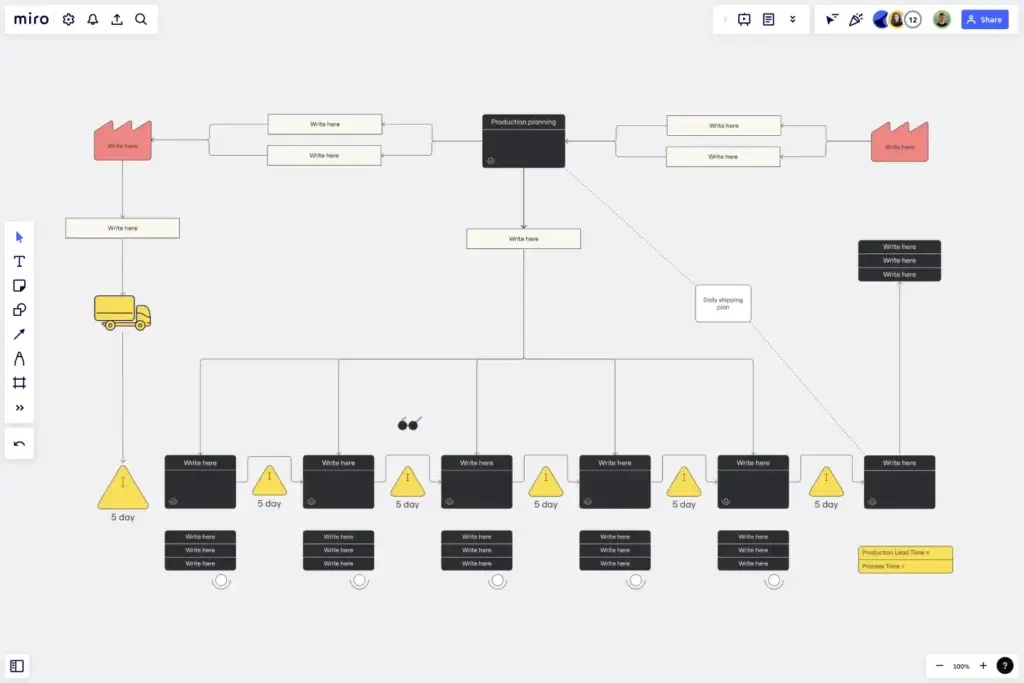
Software like Miro provide visual mapping tools to analyse the flow of materials and information, identifying areas to eliminate waste.
Pull
Process
The pull principle focuses on producing only what is needed when it is needed, driven by customer orders rather than forecasted demand. This approach minimizes overproduction and inventory costs, ensuring that resources are used efficiently and products are delivered just in time. It relies on clear signals from subsequent processes to trigger production and replenishment activities.
Comments
While the pull principle reduces waste and improves efficiency, it can also make the production system more vulnerable to disruptions in the supply chain. Relying heavily on real-time demand signals may lead to delays and shortages if there are any interruptions or inaccuracies in the information flow.
Software Analogies
Kanban Boards
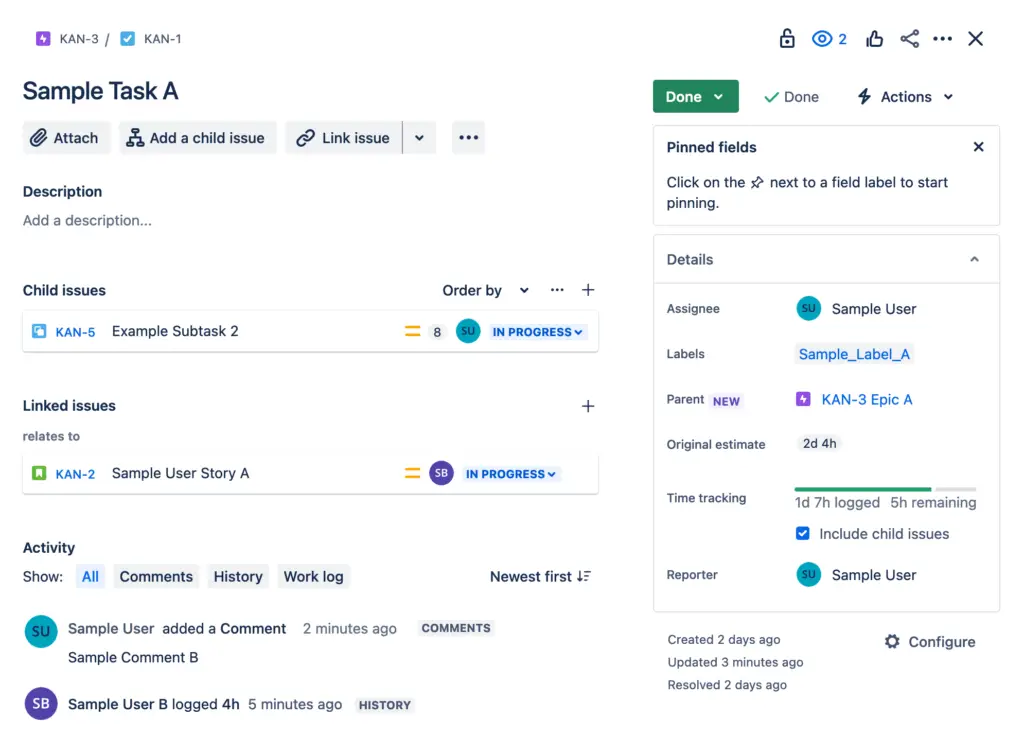
Kanban boards are used to manage workflows, allowing teams to pull tasks based on current capacity and demand.
Flow
Process
A smooth and continuous movement of products through the production process is aimed at and reffered to as flow. All necessary steps follow closely in sequence without delays or bottlenecks, minimizing waiting times to maintain a steady production pace. Achieving flow involves synchronising processes, balancing workloads, and eliminating waste.
Software Analogies
Task Automation
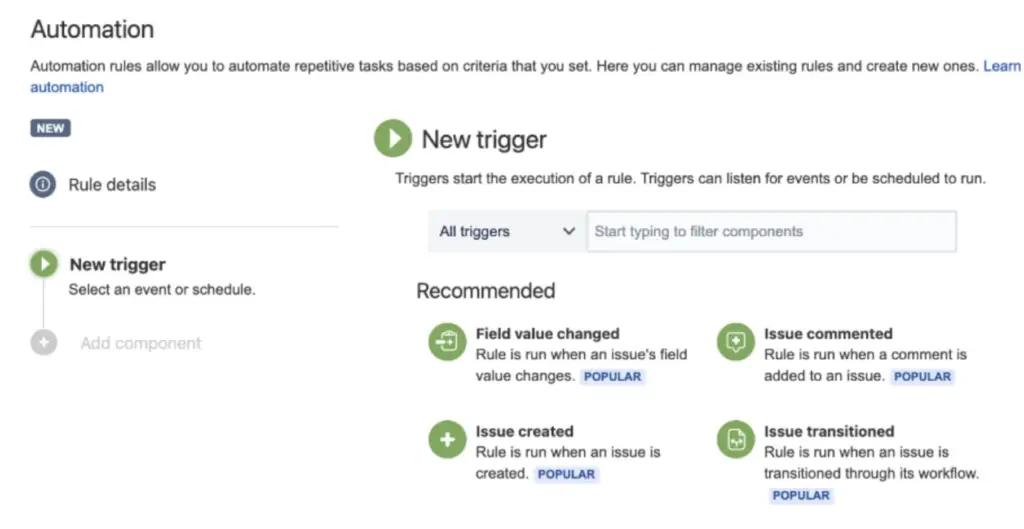
Streamlines processes by automating repetitive tasks. Repetitive tasks and actions can be automated by setting specific conditions.
Process Mapping Tools
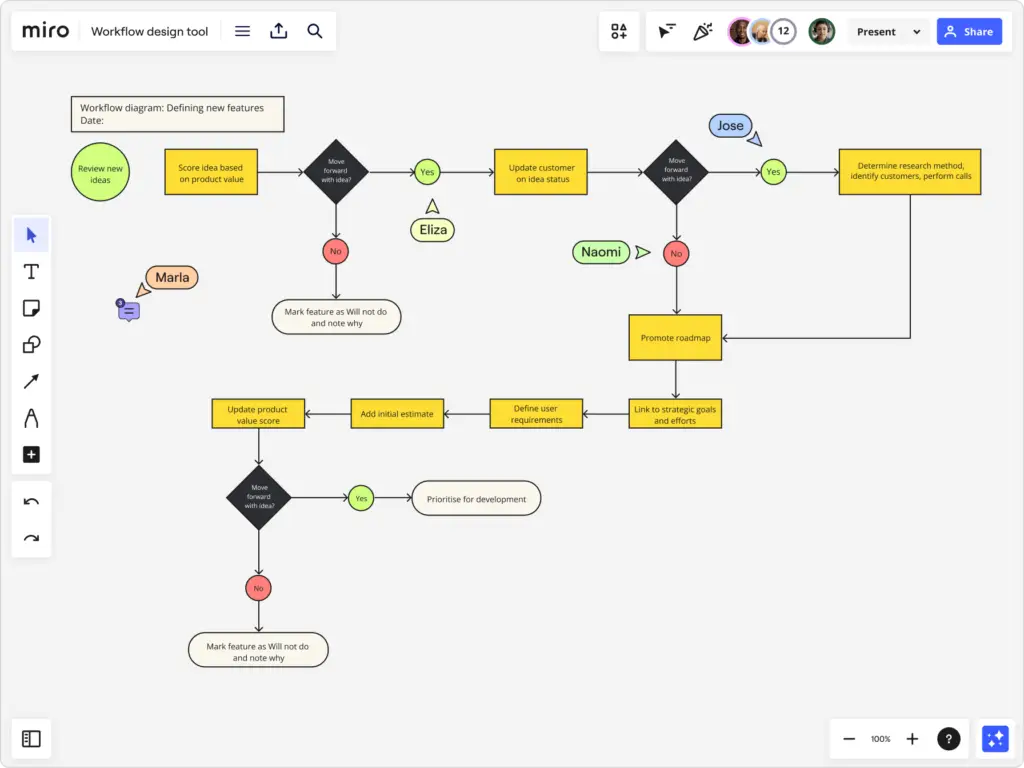
Software like Lucidchart and Miro create visual maps of workflows, allowing teams
Methods
Just-in-Time
Process
Originating from cybernetics, the Just-in-Time (JIT) system focuses on producing and delivering products exactly when they are needed, in the quantities required, and without holding excess inventory. This approach aims to reduce waste and keep production in continuous motion, similar to an information flow.
Comments
To reduce slack, the assembly line at Toyota did not have any buffer zones like in traditional Fordism. This reduced break times for workers and resulted in a more stressful working day.
Software Analogies
Inventory Management Software
Tools like Zoho Inventory manage stock levels in real-time, ensuring inventory is kept to a minimum and replenished based on actual demand.
Kanban
Process
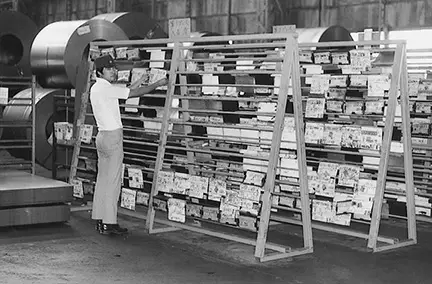
As JIT production makes the supply chain more susceptible to disruptions, a precise coordination and communication within the supply chain. The main tool for this is the visual control system Kanban, which means „signboard“ in Japanese. Manual cards on a board represent tasks and their status, which circulate between workers. The number of active cards is limited to reduce work in progress. Kanban aims to maintain a smooth flow of production, with materials arriving just in time for the next stage of the process.
Comments
Kanban enforces constant activity and responsiveness, as workers must keep up with the demands signaled by the kanban cards. Additionally, the visual nature of Kanban boards requires regular updates and accurate task representation, which can be complex and time-consuming.
Software Analogies
Kanban Boards
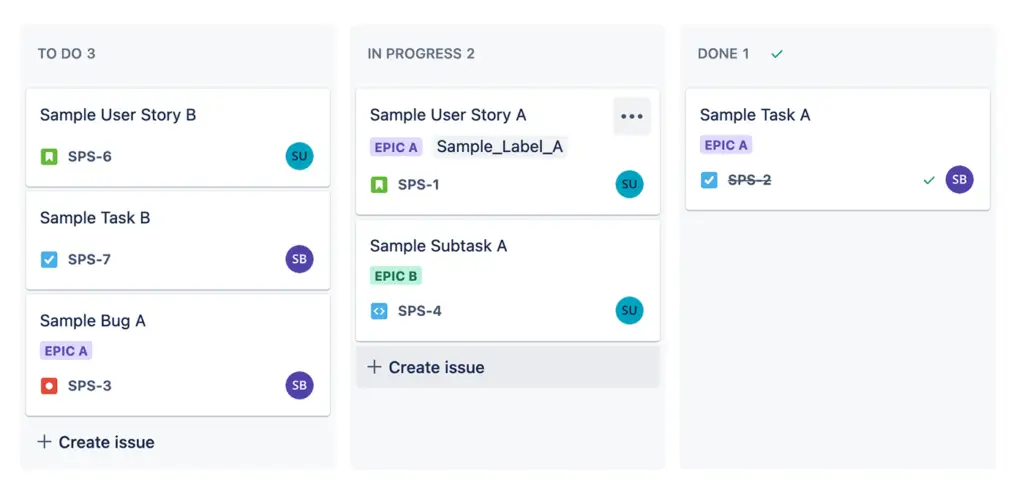
Tools like Trello and Jira use digital Kanban boards to visualise tasks, track progress, and manage workflows.
Task Management Systems
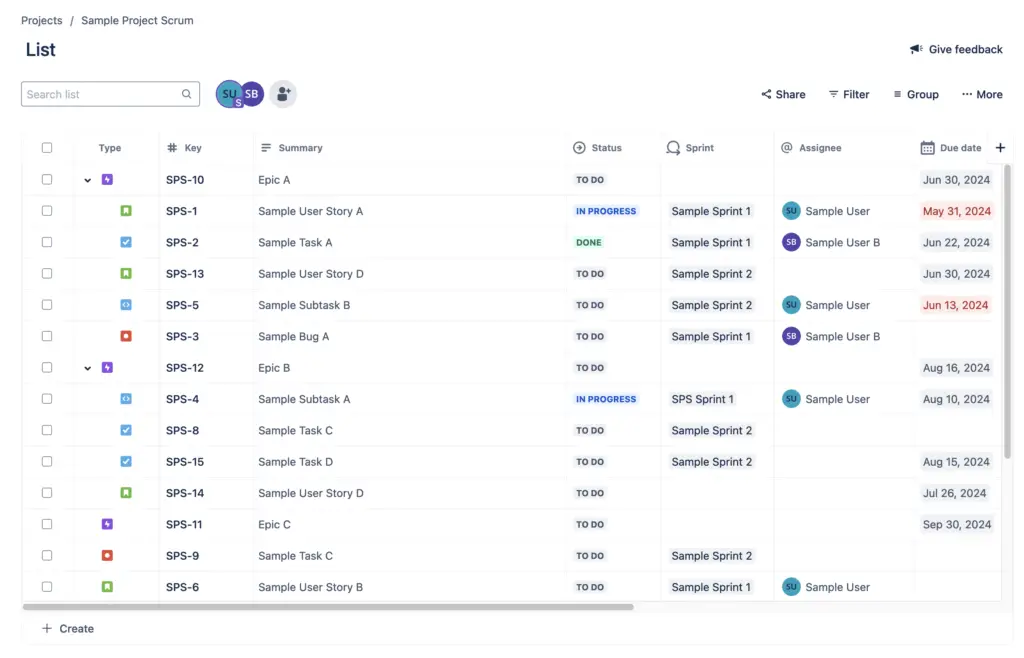
Platforms like Asana and Monday.com enable teams to create and manage tasks using Kanban-style boards, enhancing visibility and coordination.
Andon
Process
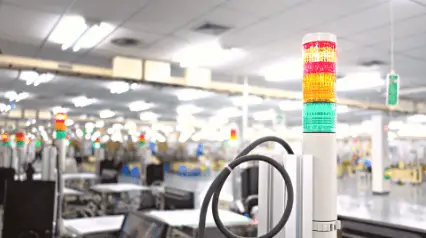
Andon is a visual management tool to provide real-time alerts and information about the status of the production line. It employs color coded lights to signal issues, which allows errors to be identified immediately and the problem to be allocated directly. Andon boards present an overview of production status, targets and key performance indicators, visible to all employees. The performance of individual teams is publicly compared by managers.
Subtask
Jidoka
Jidoka, also known as “automation with a human touch,” is a Lean manufacturing principle that focuses on building quality into the production process. It involves empowering workers and machines to detect defects and stop production immediately to address issues, preventing defects from progressing down the line.
Comments
This form of direct problem visualisation deliberately builds up pressure on the workers, creating a negative form of transparency. The public accountability can cause feelings of shame and stress.
Software Analogies
Dashboard Notifications
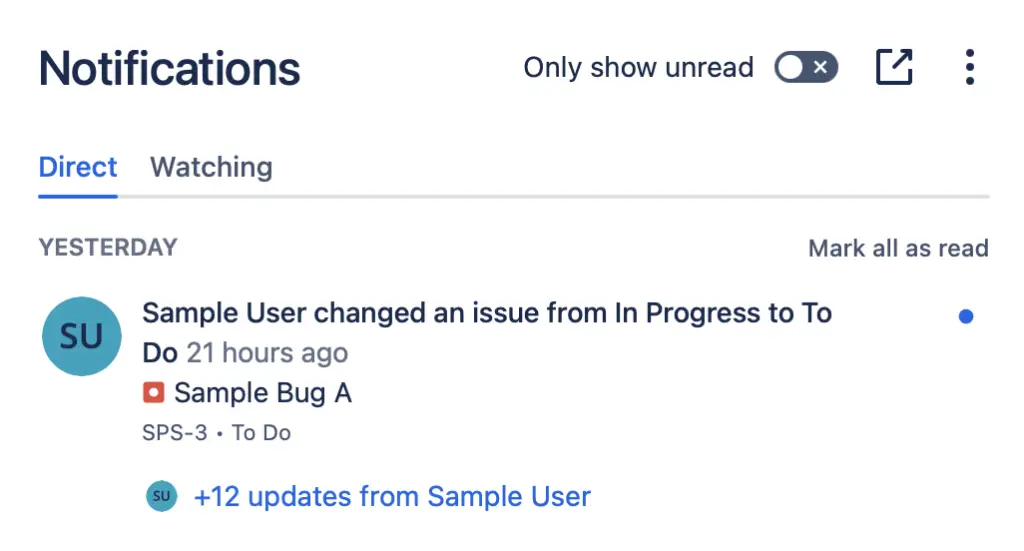
Contemporary software offers a variety of monitoring tools to deliver real-time notifications and updates. Color coded pop-up alerts highlight problems and delays, similar to Andon signals.
Emotions
Process
In Lean Production, emotions such as competition, pride or shame are strategically used as a control mechanism to motivate and regulate workers‘ behavior. Competition is actively encouraged both among individuals and groups. Workers are compared, evaluated and payed individually and are expected to evaluate other workers within an internal market.
Subtask
Point Photography
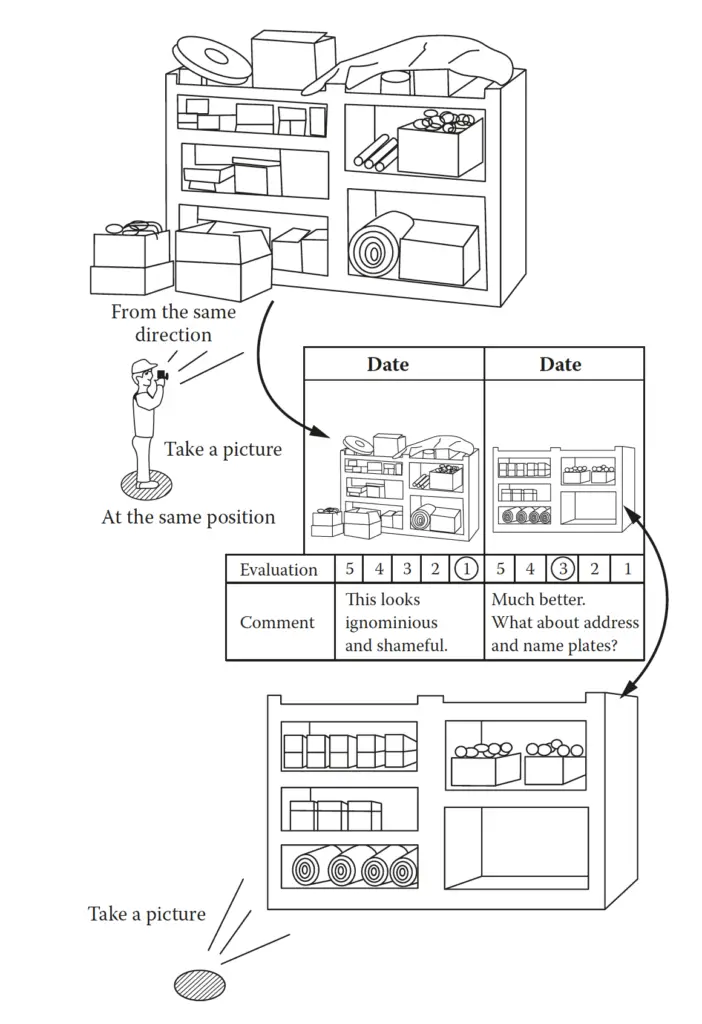
This method involves photographing workspaces recurringly and displaying them with comments on the tidiness. A photo of workers disorganised workplaces should cause shame to them, prompting them to clean and organize their area.
Comments
The emotional manipulation can cause individual blame and feelings of exploitation.
Concepts
Scrum
Process
Scrum is an Agile framework for managing complex projects, particularly in software development. It focuses on iterative progress through fixed-length sprints, typically lasting two to four weeks. Scrum involves key roles such as the scrum Master, who facilitates the process, the Product Owner, who prioritises the project backlog, and the development team, which works collaboratively to achieve sprint goals. It relies on regular ceremonies, such as sprint planning, daily stand-ups, sprint reviews, and sprint retrospectives. This framework enhances flexibility, transparency, and team collaboration, enabling quick response to changing requirements and customer feedback.
Comments
While Scrum enhances flexibility and responsiveness, it can also lead to challenges such as scope creep and team burnout if not managed effectively. The iterative nature of Scrum requires constant communication and coordination, which can be resource-intensive. Additionally, the success of Scrum heavily relies on its comprehensive implementation.
Software Analogies
Agile Software Tools
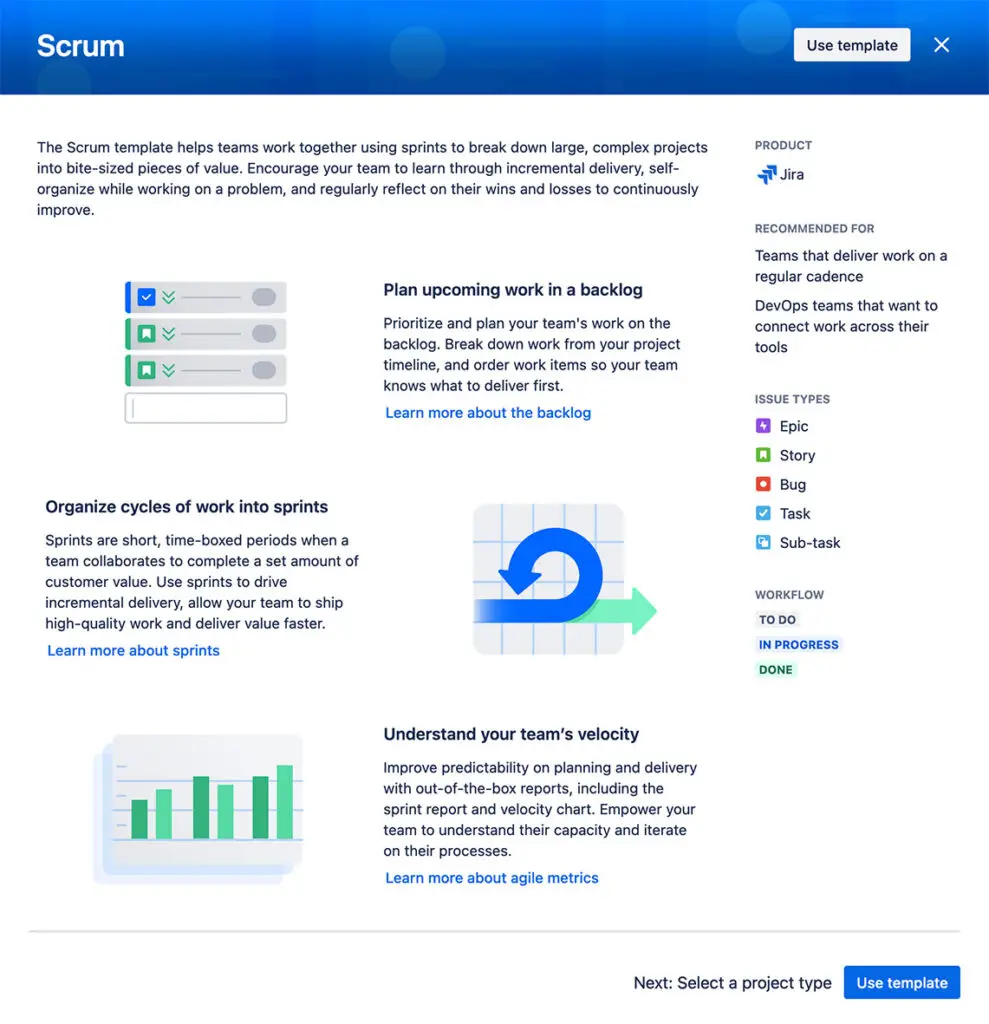
Applications like Jira, which was released one year after the publication of the Agile Manifesto in 2002, are particularly designed for agile project management. Central agile methods such as sprints or backlogs are incorporated as features into the program logic.
Design Thinking
Process
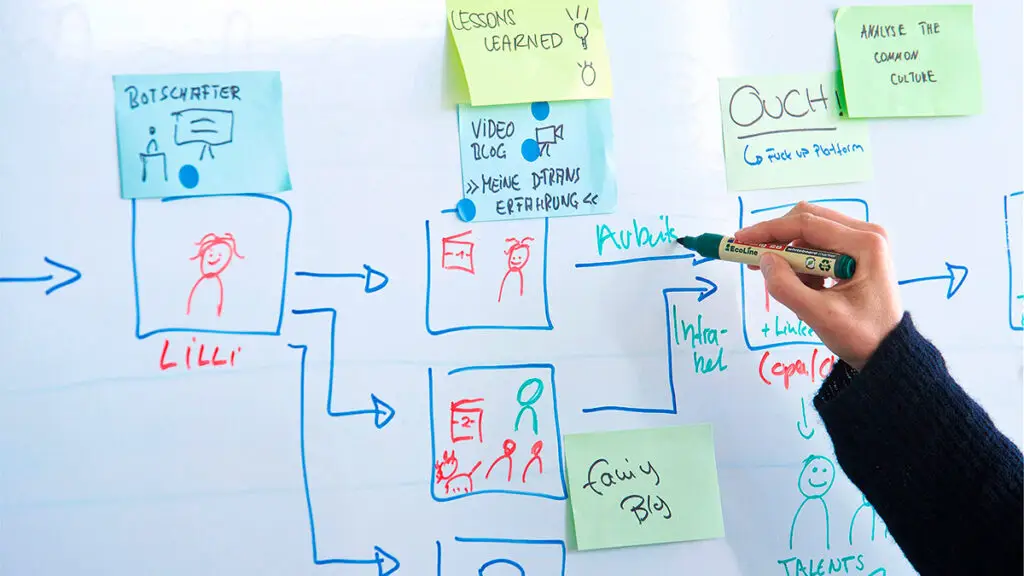
Design Thinking is an iterative, user-centered approach to problem-solving that focuses on understanding users’ needs, challenging assumptions, and redefining problems to identify alternative strategies and solutions. It involves five key stages: Empathise, Define, Ideate, Prototype, and Test. This methodology encourages creativity and innovation by involving interdisciplinary teams and prioritising user feedback throughout the development process.
Comments
The iterative process can be resource-intensive and may lead to extended development times, and without proper management, teams can struggle to transition from ideation to implementation.
Software Analogies
Collaboration Platforms
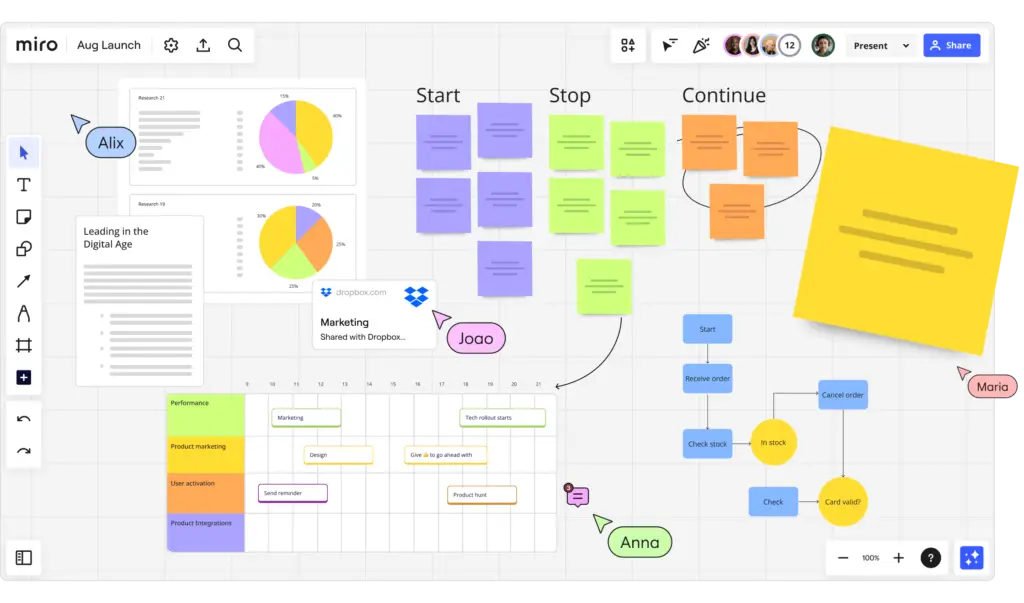
Tools like Miro facilitate visual brainstorming and ideation sessions, helping teams collaborate effectively.
Principles
Project Work
Process
Over time, project work has emerged as a classic form of post-industrial labor. A project is usually a focused effort with the clear objective of creating a new product or service, which is carried out within the limits of time, resources, and budget. Agile principles are designed for project work, which requires more flexible and innovative approaches than the regular day-to-day business.
Comments
While Agile project work promotes adaptability and responsiveness, it can also lead to challenges such as scope creep and increased pressure on team members due to continuous deadlines. The iterative nature of Agile requires constant coordination and communication, which can be demanding.
Software Analogies
Digital Project Management Tools
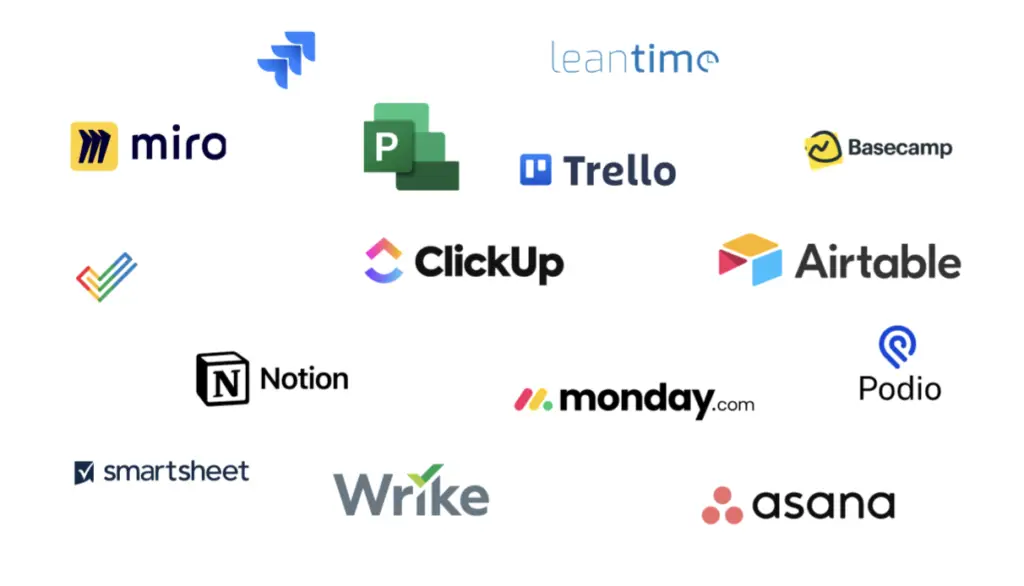
The basic common denominator of the variety of planning programmes is their design for the management of projects
Customer Centricity
Process
Customer centricity is a cruicial component of In agile work. This principle emphasises continuous feedback, iterative development, and regular adjustments based on customer input. Agile teams work closely with customers and users to understand their needs, ensuring that the final product aligns with their expectations and requirements.
Comments
Customer centricity can also lead to frequent changes and scope adjustments, potentially disrupting the development process. This approach requires robust communication and flexibility, which can be resource-intensive.
Software Analogies
Iterative Development Tools
Programmes like Jira support iterative development cycles, allowing for regular updates based on customer input.
Adaptability
Process
Agile methodologies promote a flexible approach of short term planning, which ensures the ability to adapt quickly to changes in project requirements, customer feedback, or market conditions. This principle encourages iterative development, allowing teams to make adjustments and improvements throughout the project lifecycle.
Comments
While flexibility enhances the ability to meet changing demands, it frequent changes and adjustments can disrupt workflows and increase pressure on team members. Maintaining a balance between flexibility and structure requires careful management to avoid confusion and inefficiencies.
Collaboration
Process
Collaboration in Agile involves close teamwork and continuous communication among team members to achieve project goals. Agile methodologies emphasize the importance of interdisciplinary teams working together to share knowledge, solve problems, and make decisions collectively. Regular meetings, such as daily stand-ups and sprint reviews, are essential to fostering a collaborative environment and ensuring that everyone is aligned and informed.
Comments
Collaboration can naturally cause problems such as interpersonal conflicts. The need for constant communication and coordination can be demanding and time-consuming, leading to meeting fatigue.
Software Analogies
Real-Time Collaboration
Tools like Trello or Asana enable continuous communication and information sharing among team members. They share workspaces where team members can track progress, assign tasks, and update project statuses.
Video Conferencing
Software like Zoom support regular meetings and face-to-face interactions, enhancing team cohesion and collaboration.
Methods
Small Teams
Process
Agile frameworks advocate for small, interdisciplinary teams, allowing for better communication, higher accountability, and more efficient problem-solving. This structure fosters a sense of ownership and enables faster iterations and responsiveness to changes.
Comments
Small teams can also face challenges such as limited resources and expertise. The small size may lead to a heavier workload for individual team members and potential skill gaps.
Software Analogies
Agile Planning Tools
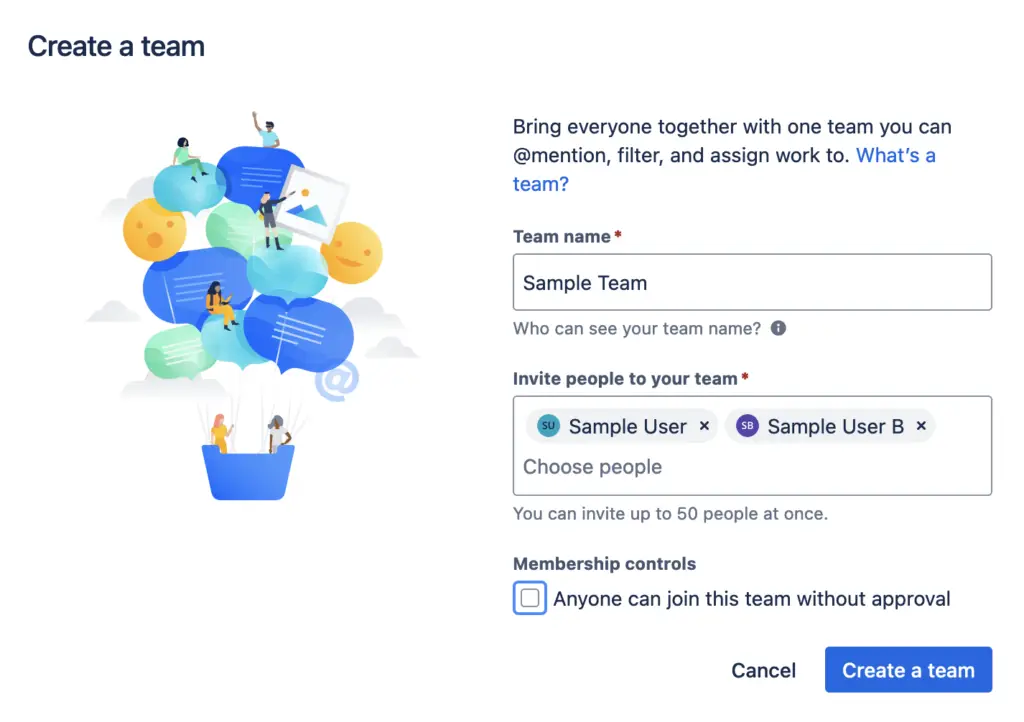
Many Software applications are particularly designes for the coordination of small teams, support effective communication and detailed task management.
Sprints
Process
Sprints are a core component of Agile methodologies, involving short, time-boxed periods (typically 2-4 weeks) during which specific work items are completed and reviewed. This iterative approach allows teams to focus on delivering incremental value, assess progress regularly, and make necessary adjustments based on feedback. Each sprint culminates in a review and retrospective to evaluate outcomes and improve processes.
Comments
A sprint can serve as a safe space for a team when it can plan its own resources autonomously and focus on core work, undisturbed and uninfluenced by higher-level positions.
The high demands on continuous delivery during frequent sprints can lead to stress, overtime, and burnout.
Software Analogies
Sprint Planning Tools
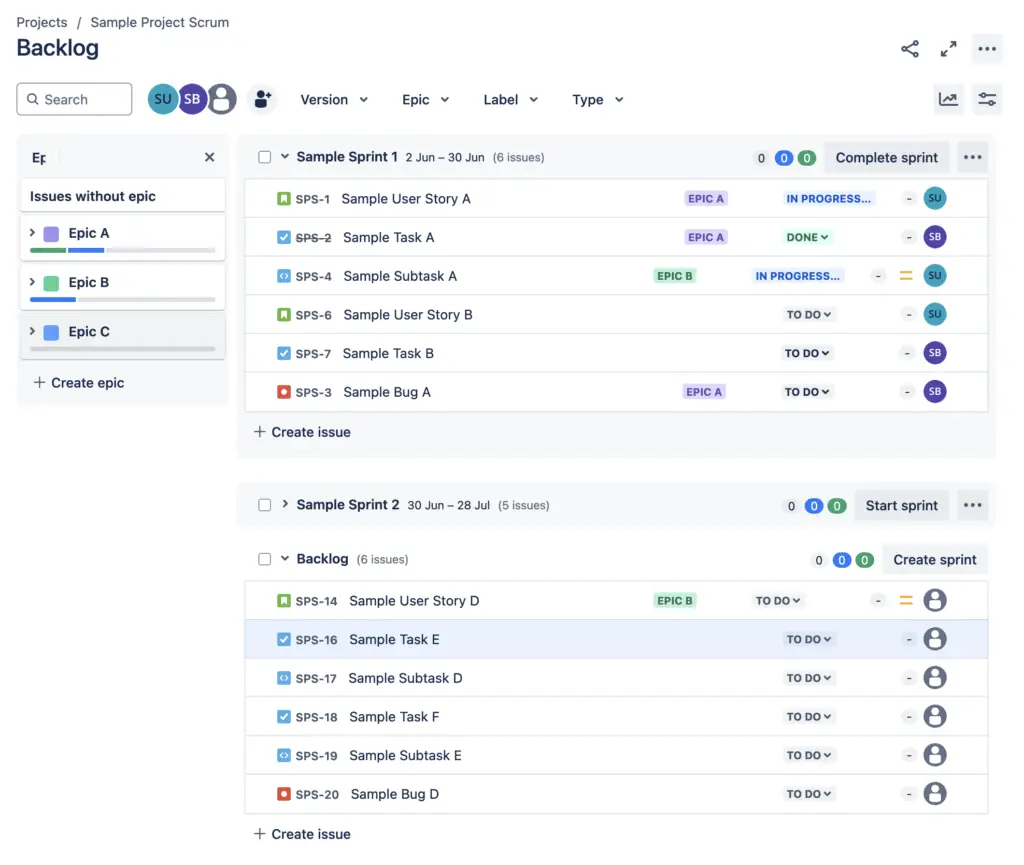
Software like Jira support sprint planning and backlog management, enabling teams to organise and prioritise work items for each sprint.
Progress Tracking
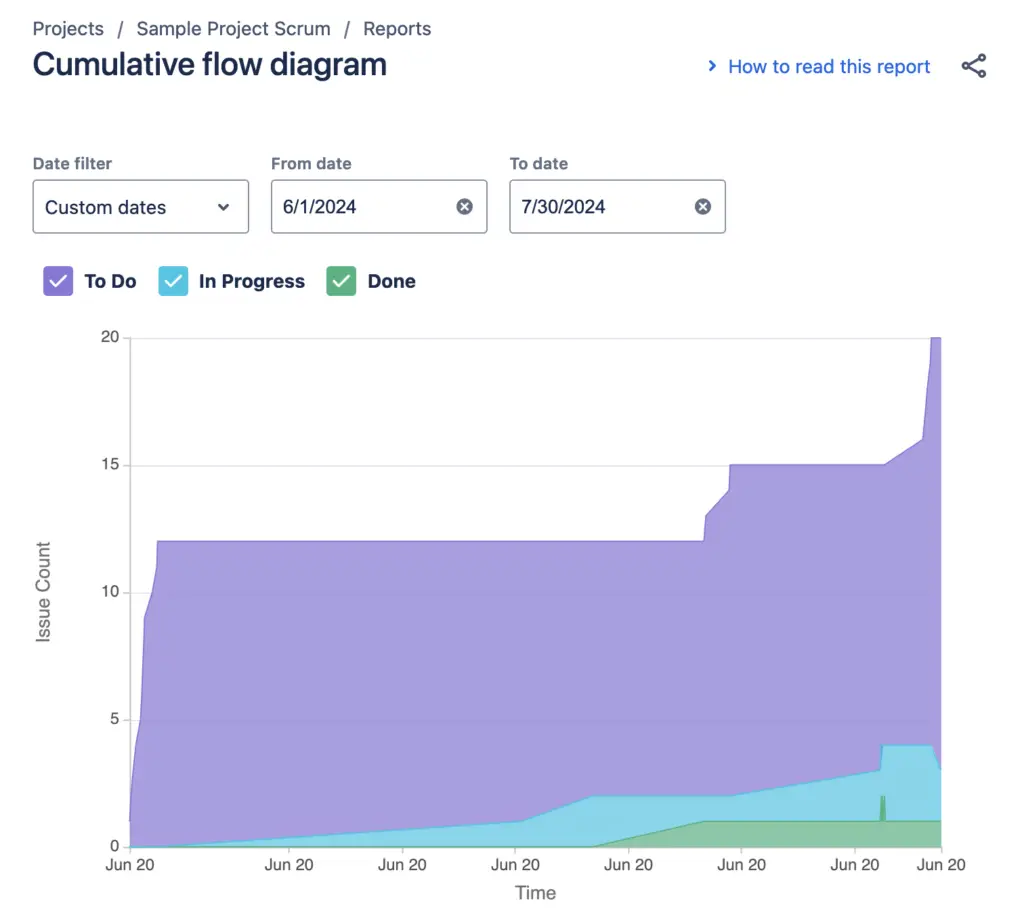
Many agile planning platforms provide visual boards and progress tracking features to monitor sprint tasks and milestones.
Retrospective Tools
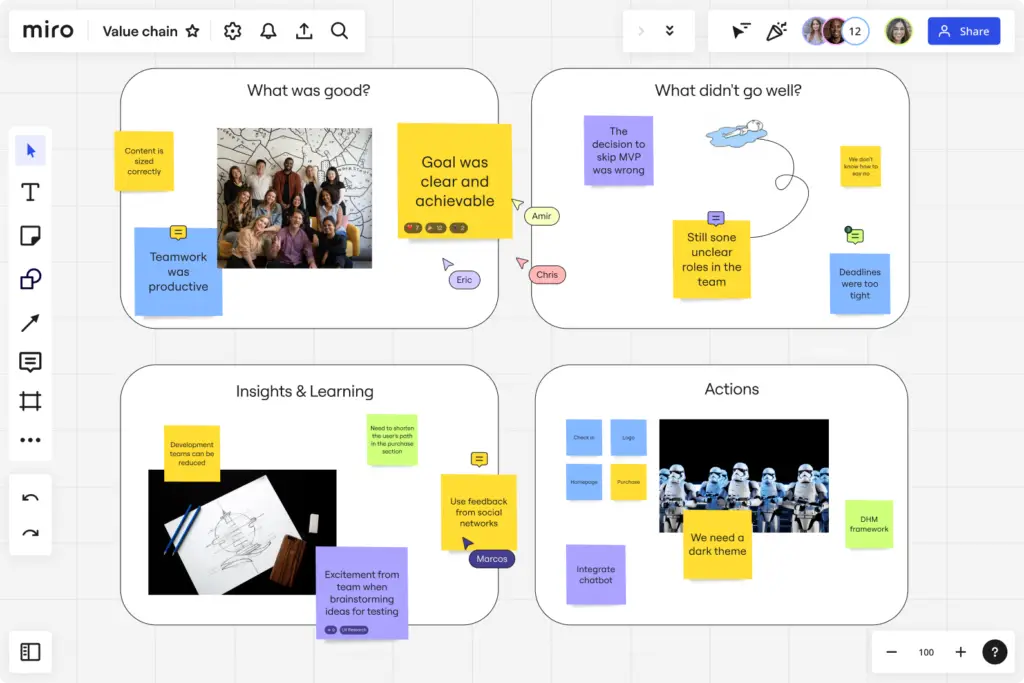
Tools like Miro offer visual templates for sprint reviews and retrospectives, which can be filled collectively.
Kanban
Process
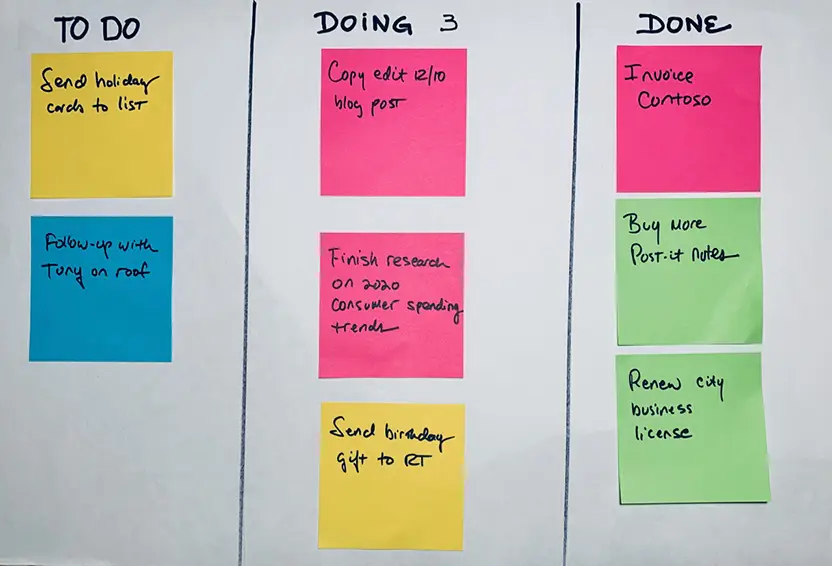
Kanban, a key component of Agile methodologies, is a visual tool that tracks and manages Tasks through various stages of a workflow. Cards are moved in a board between columns such as “To Do” or “In Progress” based on their current status. This visual transparency allows teammembers to manage work in progress effectively.
Comments
Kanban Boards can become complex if not maintained properly. The need for regular updates and accurate task representation can be time-consuming and create additional expense.
Software Analogies
Kanban Boards
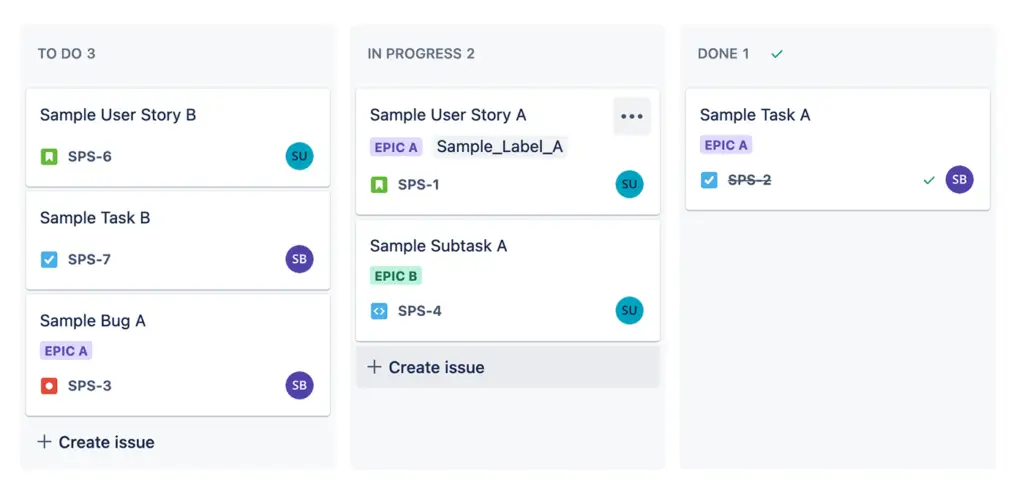
Software applications directly transformed the analogue Kanban system into a digital interface, making them a standart feature today. They Tools like Tools such as Trello utilise and promote it as their key functionality.
Backlogs
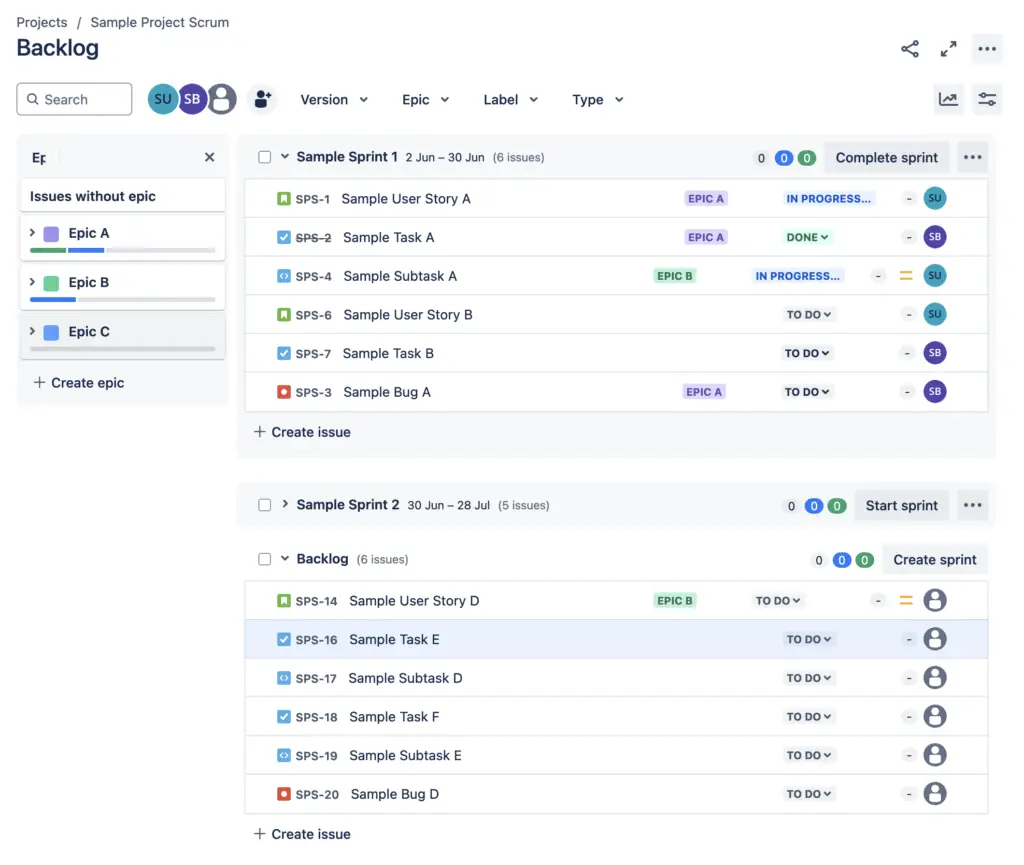
Tools like Jira provide task backlogs, allowing teams to move tasks onto the Kanban board as they are prioritised and ready to be worked on.
Iteration
Process
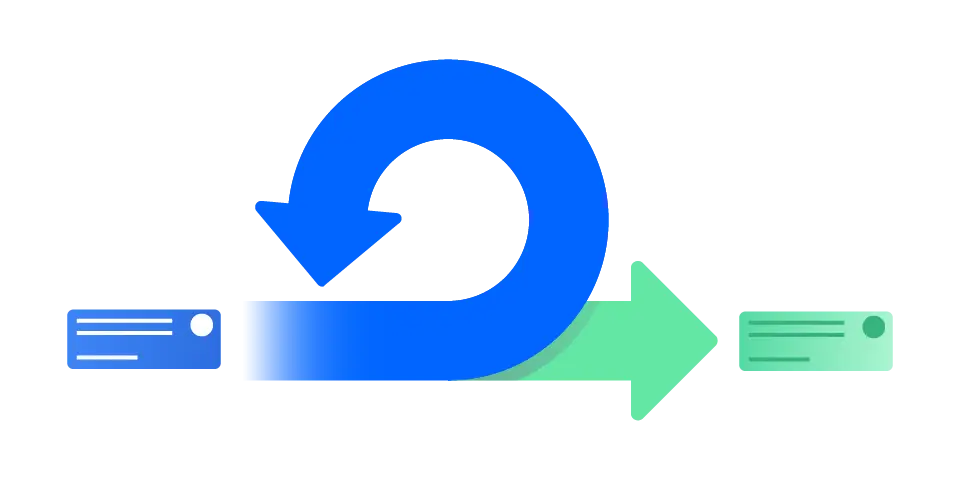
Iteration in Agile refers to the repetitive cycle of planning, developing, testing, and reviewing work in short, manageable increments. This approach allows teams to continuously refine and improve their products or processes based on feedback and evolving requirements.
Comments
The constant repetition of processes can lead to an overemphasis of the textbook orientated framework steps, where they only serve to meet the system logic itself.
Visual Management
Process
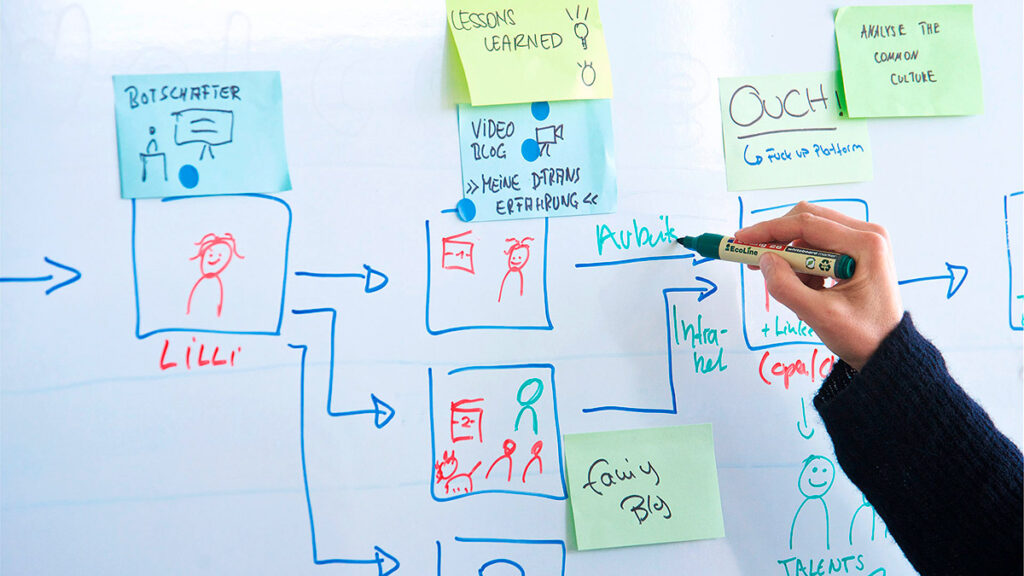
In Agile work, which emphasizes self-organization, collaboration, and democratic decision-making, visual tools play a fundamental role in enhancing transparency and communication. Key visual tools, such as maps, storyboards, or charts, help teams visualize complex ideas, providing a common visual language that clarifies ambiguities and transcends cultural and linguistic barriers.
Software Analogies
Workflow Visualization
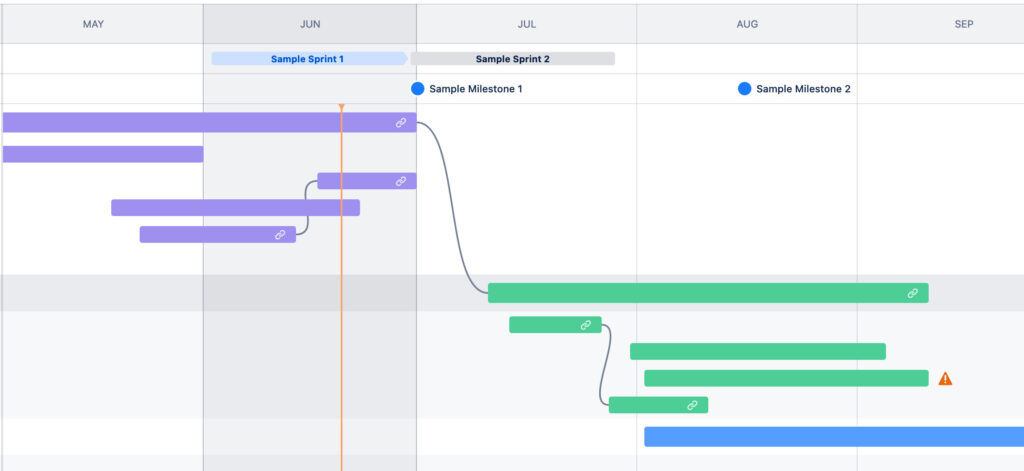
Kanban boards and Gantt charts provide visual representations of workflows. Burndown charts visualize the amount of work compared to time remaining in a sprint.
Mapping
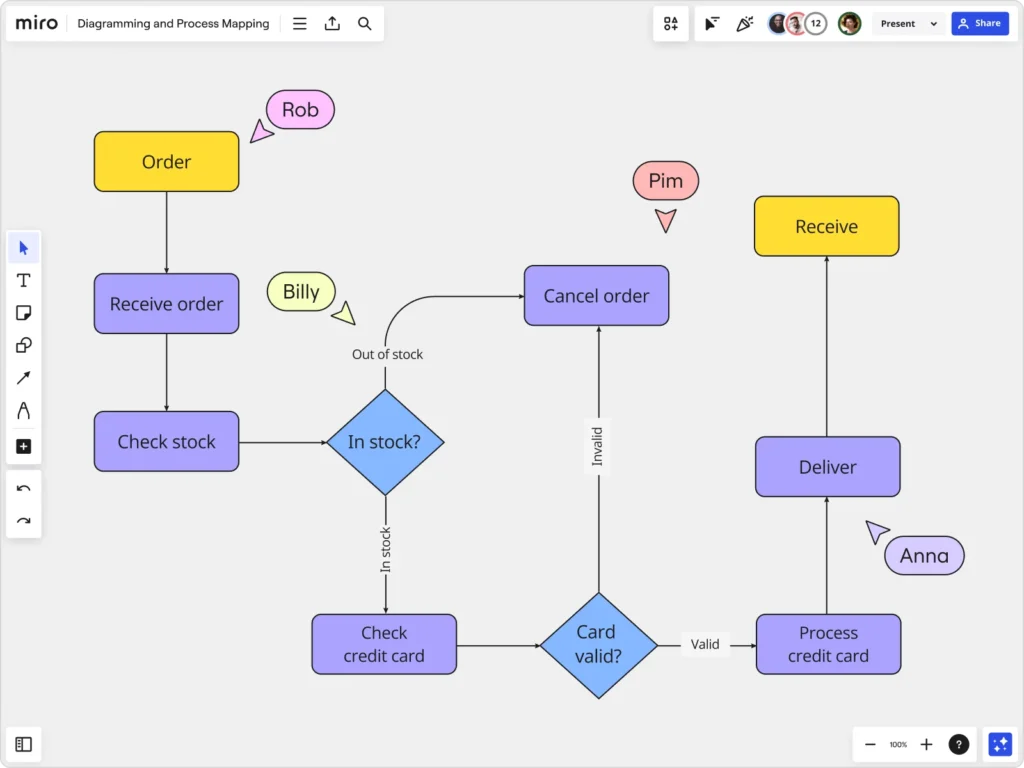
Platforms like Miro or Figjam offer templates for Roadmaps, Customer Journey Maps or Empathy Mapping.
Reports and Dashboards
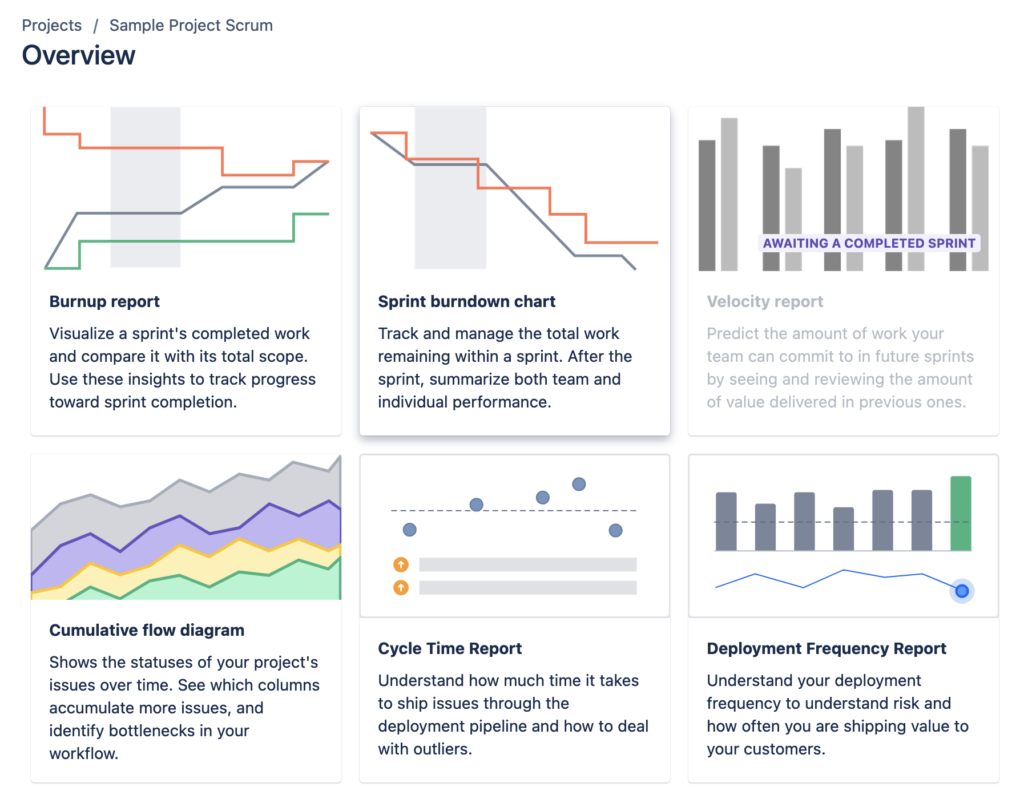
Many platforms offer customizable reports and dashboards to visualize project data, track metrics, and provide insights into team performance.